As the principle of ultrasonic cleaning is the cavitation effect, its performance verification is mainly to verify the cavitation effect, the purpose is to see whether the intensity of the sound field in the cleaning tank has a blind spot. There are many methods, here are six ways to verify the performance of ultrasonic cleaning machine for your reference.
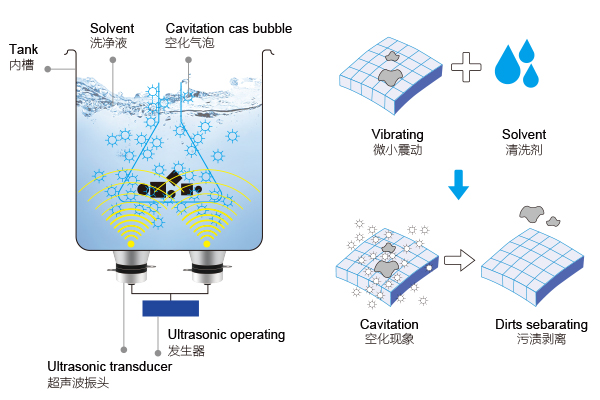
1、aluminum foil corrosion method
The thickness of 20-30μm aluminum foil fixed in a bracket, vertical into the cleaning tank, do not touch the bottom. Remove after a period of electricity, the corrosion degree of different places on the surface of the aluminum foil can indirectly reflect whether the ultrasonic strength of that depth is uniform. If you want to detect the ultrasonic intensity distribution in the horizontal direction, you can place the aluminum foil horizontally. A manufacturer’s manual states that if there is a blank spot > 1 square inch (6.45 cm2), it is a cold spot.
This method is intuitive and simple, but it does not allow for quantitative testing. The error is significant. Testing is difficult to achieve under the conditions of loading equipment and may chemically react with alkaline cleaning agents. Sometimes the whole slides will fall off, so the ultrasonic time should be set.
2、Slide washing and removal method
Use HB pencil to smear the slide every week, and ultrasonic washing is qualified if it washes off within 3min, and record the result (IAHCSMM Re-education Training Manual 2006, USA).
This method is simple to operate, but it cannot be tested quantitatively and has a large error.
3、starch potassium iodide reaction method
Consider the starch as a light-sensitive emulsion, apply it on one side of the slide, and then put it into a water bath with diluted iodine solution for ultrasound. Under the effect of ultrasonic cavitation, iodine reacts with starch to turn blue, which discolors the slide. The slides are removed for rinsing and drying. The discolored area is observed and used to infer the distribution of the acoustic field.
This method can make up for the shortcomings of aluminum foil damage in the aluminum foil etching method, but it cannot be quantitatively detected.
4、Dyeing method
Configure the dye (such as methylene blue dye) in water, put the copper plate paper into the water ultrasonic, under the effect of ultrasonic cavitation, the dye will adhere to the paper, remove the paper, rinse and dry, observe the dye pattern on the background of the paper sheet used to assess the distribution of the sound field. If the distribution is not uniform, it means that the sound field is not uniform and there are cold spots.
5、Ultrasonic energy bottle test
SonoCheck ultrasonic energy bottle can be used to verify the cavitation ability of ultrasound, the time required is proportional to the cavitation ability of ultrasound. According to the volume of the tank, arrange the arrangement points at different locations, place the energy bottle and observe the discoloration time.
This method is intuitive and simple, but it is also a qualitative measurement.
6、 Ultrasonic energy analyzer
Inserted directly into the solution, the intensity of ultrasonic energy and the distribution of ultrasonic energy density can be detected quantitatively.
In practice, the above methods can be used as the department’s own monitoring methods, each with its own advantages and disadvantages. Ultrasonic cleaning machine is only one part of the cleaning process, our goal is to ensure the quality of cleaning. Therefore, it is also essential for the establishment, optimization and compliance of the process.