With the development of industry, ultrasonic cleaning machine cleaned by the workpiece more and more fine, the requirements of the workpiece cleanliness is also increasingly high, so how to correctly select the frequency and power of ultrasonic cleaning is vital, but many friends are at a loss, do not know how to correctly select the power and frequency of ultrasonic cleaning machine.
Ultrasonic cleaning machine power selection
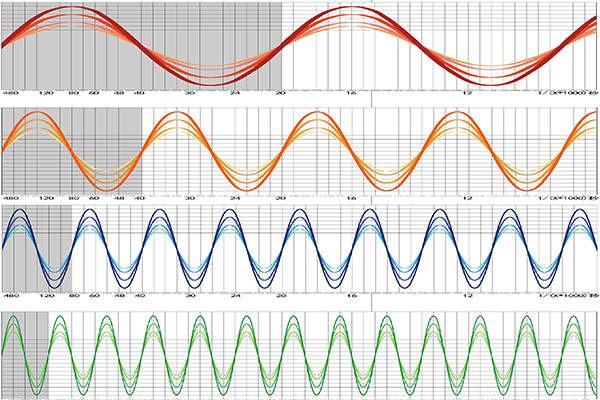
The ultrasonic power in the cleaning tank determines the size of the sound intensity in the sound field, and the size of the sound intensity directly affects the effect of cavitation, therefore, to choose the appropriate ultrasonic power.
If the main medium of cleaning with water, ultrasonic cleaning power reference data.
Cleaning optical glass liquid crystal products, ultrasonic power of 10 ~ 20W / L.
Cleaning precision instrument components, ultrasonic power of 20 ~ 25W / L.
Cleaning metal internal pressure parts, ultrasonic power is 25~30W/L.
For cleaning powder metallurgy parts and fine casting parts, the ultrasonic power is 30~35W/L.
For injection molding devices, due to the complexity of the components, itself is the sound-absorbing body, ultrasonic power in 35W / L or more.
Ultrasonic cleaning effect is not necessarily completely proportional to the power, cleaning time. For a workpiece adhering to dirt, if the cleaning machine power is not enough, then spend more time, the washing effect is also very limited, the power is appropriate, dirt immediately removed. Ultrasonic power is too large, although the cleaning effect is obvious, but may make the precision workpiece surface etching points, the oscillator work surface will also produce cavitation corrosion, which should be avoided. Too much sound intensity will cause too many cavitation bubbles. Increase scattering attenuation, the formation of acoustic barriers, so that sound waves do not easily spread throughout the liquid space, away from the sound source, can not form a balanced cleaning, how to choose ultrasonic power, need to be based on the shape of the workpiece material, the nature of the cleaning fluid, process and other comprehensive considerations.
Ultrasonic cleaning machine frequency selection
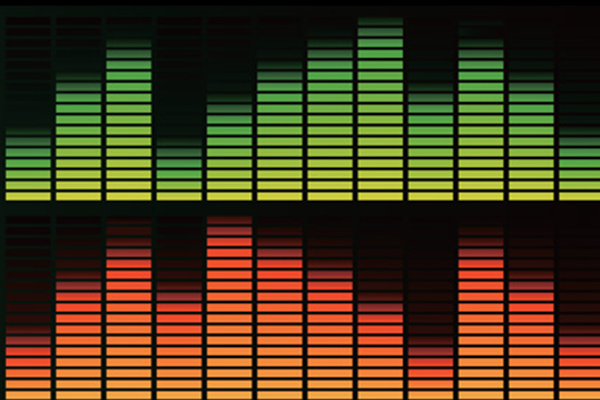
In conventional cleaning, the frequency selection is generally in the range of 20 ~ 40 kHz and 68 ~ 120 kHz two segments. In the low frequency band formed in the cavitation bubble radius is larger, collapse when the strength is also large, but not uniform enough, suitable for removing 3 ~ 5 um of dirt particles. The higher the frequency, the higher the cavitation threshold, that is, the greater the sound intensity required for cavitation, and the finer and more uniform the formation of cavitation bubbles.
Low frequency band is suitable for cleaning the surface of large workpieces and dirt and cleaning surface bonding strength of high occasions, but not easy to penetrate deep holes and surface shape of complex components. While the high frequency band cavitation intensity “mild”, noise is small, the chemical bubble is relatively dense and uniform, you can drill parts with complex shapes, slits, deep holes, blind holes in the parts for cleaning.
In practice, ultrasonic cleaning frequency reference data.
Powder metallurgy parts such as magnetic cores, magnetic rings, with grinding magnetic powder class, choose a frequency of 20 ~ 25 kHz.
Rough machining of metal parts, such as automotive wheels, cylinder components and other large parts, select a frequency of 25 ~ 28 kHz.
for watch parts, precision stampings, a frequency of 40 kHz is suitable for selection.
For optical glass, low-grade liquid devices, a frequency of 68 to 120 kHz is suitable for selection.
For semiconductor silicon wafers, liquid crystal glass substrate cleaning electrode lead width of 8 pm, or line spacing of 8 pm, the requirement to remove 1 ~ 3 pm of dirt particles, you need to choose 0.8 ~ 1.0 MHz of flowing megahertz ultrasonic cleaning.
Currently, in the ultrasonic cleaning process, less use of a single frequency, often two or more frequencies. Rough cleaning with a lower ultrasonic frequency, fine cleaning with a higher ultrasonic frequency, and all with a sweep function. Cleaning process used in the method is also more, there are compound cleaning, alternating between respect cleaning or with dual-frequency transducer frequency hopping cleaning, which helps to improve the quality of cleaning and productivity.