After metal processing, the cleaned objects are left with residual oil stains that form different oil stains. These oil stains can affect the subsequent surface treatment process and reduce the bonding of the coating to the substrate. Therefore, in order to improve the appearance quality, performance, life span and meet the needs of the next process, a strict cleaning procedure is necessary. Before cleaning, the choice of cleaning agent is a very important point, it will directly affect the cleaning effect. Therefore, according to the material structure and shape of the workpiece to be cleaned, the nature of dirt and cleanliness requirements, carefully select the appropriate cleaning agent.
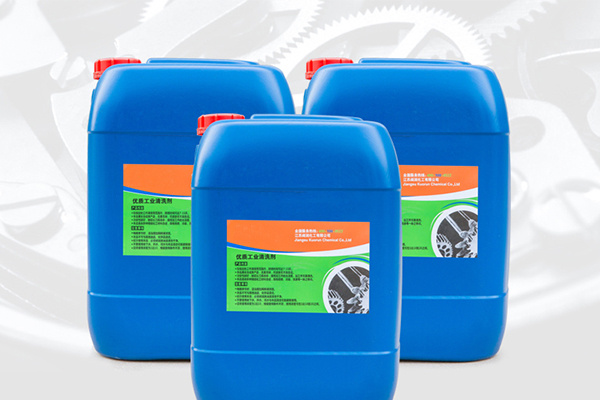
The hydrocarbon cleaning agent widely used in the market is mainly used to clean the residual oil after metal processing, including stamping oil, wire drawing oil, cutting oil and tapping oil. Next, we will introduce the working environment of these four oils in detail.
1、Punching oil: Punching oil is suitable for punching, punching, tapping, tapping and other high-intensity operations. It is also suitable for plastic forming processing. It has good lubricity and extreme pressure, and has good protection performance for dies. General workpiece temperature rise is not big, you can use mineral oil, but deep punching processing, large workpiece stretching processing and other temperature rise is big, adding extreme pressure anti-wear agent is necessary. And in the cold forging process, the temperature rise is very high, but also add solid lubricant or dry film lubricant.
2、Drawing oil: drawing oil is used for metal stamping processing. It has excellent wear resistance and extreme pressure. It will not cause workpiece strain and strain to the workpiece. It can improve the workpiece finish and effectively prolong the die life.
3、Cutting oil: cutting oil has very good performance of thorough protection for CNC machine tool itself, cutting tools and workpiece. In the metal cutting process, cutting each time in the newborn surface, speed changes a few millimeters per minute to hundreds of meters, pressure up to 2 ~ 3GPa. cutting in addition to friction, there are tools and cutting into the metal internal molecular friction, cutting area interface temperature up to 600 ~ 800 ℃. Such high temperature and high pressure will reduce the strength and hardness of the tool, so the cutting oil must be both cooling, lubrication, cleaning and rust prevention four roles.
4, tapping oil: tapping oil lubricity is extremely high, can effectively reduce the cutting temperature, so as to obtain a greater cutting accuracy, suitable for stainless steel, alloy steel, ferrous metals, non-ferrous metal products tapping, tapping and other processes of lubrication. For high difficulty tapping occasions, also has an effective lubrication and cooling effect. It can also be applied to the difficult cutting of various hard-to-process materials, such as high-speed turning, drilling, tapping, broaching, hobbing and tooth planing of stainless steel and heat-resistant steel.
The above is to introduce the working environment of stamping oil, drawing oil, cutting oil and tapping oil. These four types of oil produced by the oil stains, with hydrocarbon cleaning agent can be well cleaned.