Ultrasound cleaning is a highly efficient and widely used method for removing contaminants from surfaces, particularly in industries such as healthcare, manufacturing, and jewelry. This technology relies on high-frequency sound waves to create cavitation bubbles in a cleaning solution, which implode and dislodge dirt, grease, and other particles. To fully grasp the intricacies of ultrasound cleaning, it is essential to understand the terminology and supplementary information that define its processes and applications.
This article delves into the core concepts, advanced terms, and practical appendices that are critical for anyone working with or studying ultrasound cleaning technology.
The Science Behind Ultrasound Cleaning
Ultrasound cleaning operates on the principle of cavitation, a process where sound waves generate microscopic bubbles in a liquid. These bubbles grow and collapse, releasing energy that scrubs surfaces clean. The frequency of the sound waves plays a significant role in determining the cleaning effectiveness. Lower frequencies (20-40 kHz) produce larger bubbles, suitable for heavy-duty cleaning, while higher frequencies (40-80 kHz or more) create smaller bubbles, ideal for delicate items.
The cleaning solution, or solvent, is another critical component. It enhances the cavitation process by reducing surface tension and dissolving contaminants. Common solvents include water-based solutions, alkaline cleaners, and specialized degreasers.
Key Terminology in Ultrasound Cleaning
1. Cavitation
Cavitation refers to the formation, growth, and implosion of bubbles in a liquid due to pressure changes caused by sound waves. This phenomenon is the backbone of ultrasound cleaning, as the energy released during bubble collapse dislodges contaminants.
2. Frequency
Frequency, measured in kilohertz (kHz), determines the size and intensity of cavitation bubbles. Lower frequencies are used for robust cleaning tasks, while higher frequencies are preferred for precision cleaning.
3. Transducer
A transducer is the device that converts electrical energy into mechanical vibrations, producing the sound waves necessary for cavitation. Piezoelectric transducers are commonly used in ultrasound cleaning systems.
4. Cleaning Solution
The cleaning solution, or solvent, is the liquid medium in which cavitation occurs. Its composition varies depending on the type of contaminants and the materials being cleaned.
5. Degassing
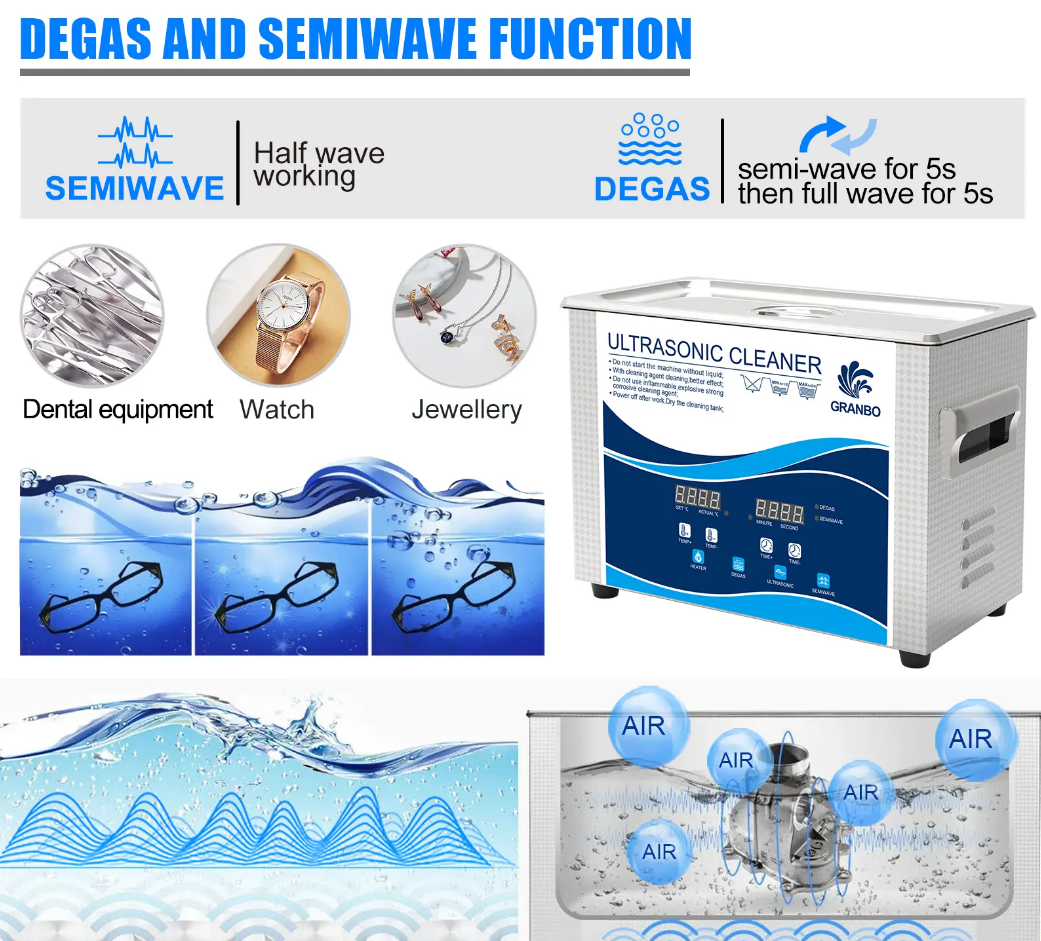
Degassing is the process of removing dissolved gases from the cleaning solution. Excess gases can dampen cavitation, reducing cleaning efficiency.
Practical Applications of Ultrasound Cleaning
1. Medical and Dental Instruments
Ultrasound cleaning is indispensable in healthcare for sterilizing surgical tools, dental instruments, and other medical devices. Its ability to reach crevices and hard-to-access areas ensures thorough cleaning.
2. Jewelry and Watches
Jewelers rely on ultrasound cleaners to remove dirt, oils, and polishing compounds from intricate pieces without causing damage.
3. Automotive and Aerospace
In these industries, ultrasound cleaning is used to degrease engine parts, clean fuel injectors, and remove contaminants from aerospace components.
4. Electronics
Ultrasound cleaning is employed to remove flux residues, dust, and other contaminants from printed circuit boards (PCBs) and electronic assemblies.
5. Manufacturing
Manufacturers use ultrasound cleaning to prepare metal surfaces for coating, painting, or welding, ensuring optimal adhesion and quality.
Appendix: Troubleshooting and Maintenance
1. Common Issues and Solutions
– Reduced Cleaning Efficiency: This may be due to insufficient power density, improper frequency, or a contaminated cleaning solution. Regularly check and adjust these parameters.
– Damage to Delicate Items: Use higher frequencies and lower power densities for fragile components.
– Excessive Noise: Ensure the cleaning tank is properly insulated and the transducer is functioning correctly.
2. Maintenance Tips
– Regularly replace or filter the cleaning solution to maintain its effectiveness.
– Inspect and clean the transducer to prevent performance degradation.
– Calibrate the system periodically to ensure optimal operation.
3. Safety Precautions
– Always wear protective gear when handling cleaning solutions, especially those containing harsh chemicals.
– Avoid prolonged exposure to ultrasound waves, as they may cause hearing damage.
The Future of Ultrasound Cleaning Technology
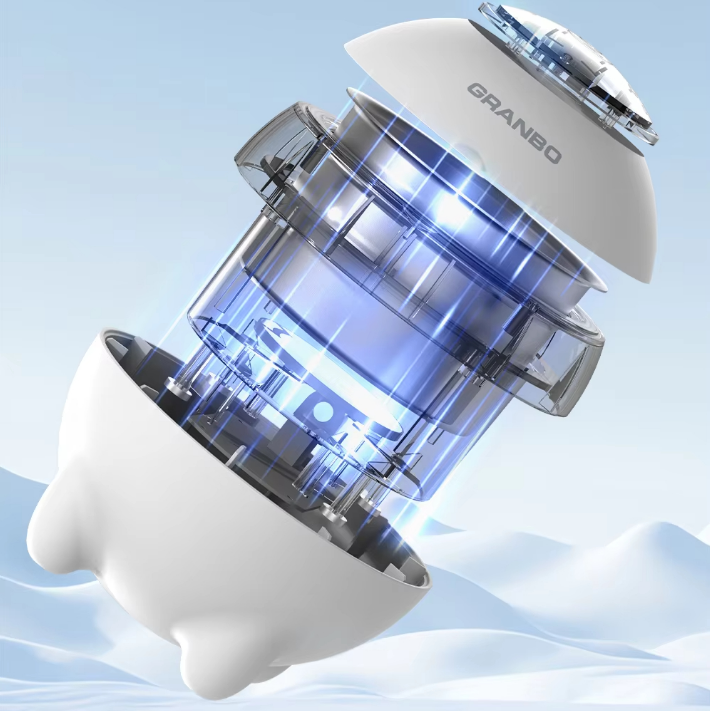
As industries continue to demand higher precision and efficiency, ultrasound cleaning technology is evolving to meet these needs. Innovations such as AI-driven cleaning systems, eco-friendly solvents, and advanced frequency modulation are paving the way for smarter, more sustainable cleaning solutions.
By understanding the terminology, advanced concepts, and practical applications of ultrasound cleaning, professionals can harness its full potential to achieve superior cleaning results.
References
1. Mason, T. J., & Lorimer, J. P. (2002). *Applied Sonochemistry: Uses of Power Ultrasound in Chemistry and Processing*. Wiley-VCH.
2. Ensminger, D., & Bond, L. J. (2011). *Ultrasonics: Fundamentals, Technologies, and Applications*. CRC Press.
3. Gallego-Juárez, J. A., & Graff, K. F. (2015). *Power Ultrasonics: Applications of High-Intensity Ultrasound*. Woodhead Publishing.
4. FDA Guidelines on Medical Device Cleaning. U.S. Food and Drug Administration.
5. ASTM International Standards for Cleaning Processes. ASTM Committee G01.