Understanding Multi-Ultrasonic Transducers
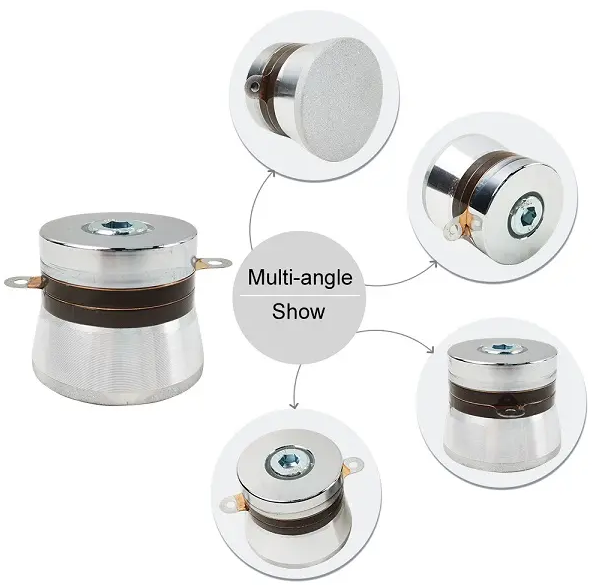
Ultrasonic technology has transformed cleaning, welding, and medical imaging by using high-frequency sound waves to perform precise and efficient tasks. At the heart of these systems are ultrasonic transducers—devices that convert electrical energy into ultrasonic waves. While single-transducer systems have been widely used for decades, multi-ultrasonic transducer setups are becoming increasingly popular due to their superior cleaning efficiency, uniformity, and adaptability.
Multi-ultrasonic transducer systems integrate multiple transducers within a single unit, either arranged in an array or strategically placed around an object to ensure even distribution of ultrasonic waves. This results in improved cavitation effects, higher cleaning power, and greater versatility for industrial, medical, and commercial applications.
How Multi-Ultrasonic Transducers Work
1. The Role of Cavitation in Ultrasonic Cleaning
Cavitation is the key mechanism in ultrasonic cleaning. When ultrasonic waves pass through a liquid, they create microscopic bubbles that rapidly expand and collapse. This process generates high-energy micro-jets that effectively remove dirt, grease, and contaminants from surfaces, even in hard-to-reach areas.
2. Advantages of Multiple Transducers
Unlike single-transducer systems, which concentrate ultrasonic waves in one direction, multi-transducer setups distribute energy across a broader area. This improves cleaning uniformity, reduces dead zones, and enhances the ability to clean complex or large objects. Additionally, multi-frequency transducers can be incorporated to optimize cleaning for different materials and contamination types.
3. Frequency Variations for Precision Cleaning
Multi-ultrasonic transducer systems can operate at multiple frequencies, typically ranging from 20 kHz to 200 kHz. Lower frequencies produce larger cavitation bubbles for heavy-duty cleaning, while higher frequencies generate finer bubbles for delicate surfaces such as medical instruments, optical lenses, and electronic components.
Key Benefits of Multi-Ultrasonic Transducer Systems
1. Enhanced Cleaning Uniformity
One of the biggest advantages of multi-transducer systems is the ability to eliminate dead zones. With multiple transducers strategically placed within a cleaning tank, the ultrasonic waves are evenly distributed, ensuring all parts of an object receive consistent cleaning power.
2. Increased Efficiency and Power
Multi-transducer setups generate higher ultrasonic power, improving the speed and effectiveness of cleaning. This reduces processing time for industrial and commercial applications, making operations more efficient.
3. Versatility for Different Applications
Multi-frequency transducers allow users to customize cleaning processes based on the material and type of contamination. For instance, a combination of 25 kHz and 80 kHz transducers can handle both heavy-duty degreasing and fine-detail cleaning in a single system.
4. Greater Scalability and Customization
Industries with varying cleaning needs benefit from multi-transducer systems because they can be customized to specific requirements. Whether for small medical tools or large automotive parts, these systems can be tailored to fit different tank sizes and cleaning intensities.
5. Reduced Chemical Dependency
Because multi-ultrasonic transducer systems enhance cavitation efficiency, they often require fewer chemical detergents. This makes them an environmentally friendly alternative to traditional cleaning methods.
Applications of Multi-Ultrasonic Transducers
1.Medical and Healthcare Industry
Hospitals and laboratories use ultrasonic cleaning to sanitize surgical instruments, dental tools, and endoscopic equipment. Multi-transducer systems ensure thorough sterilization by reaching microscopic crevices where contaminants may linger.
2.Electronics and Semiconductor Cleaning
Ultrasonic cleaning is essential for removing flux residues, dust, and oxidation from circuit boards, semiconductor wafers, and precision components. Multi-transducers help prevent damage to delicate electronic parts by providing controlled cavitation intensity.
3.Automotive and Aerospace Industries
From fuel injectors to turbine blades, ultrasonic cleaning plays a vital role in maintaining engine components. Multi-ultrasonic transducers improve efficiency in removing carbon buildup, grease, and machining residues from intricate metal parts.
4.Jewelry and Watchmaking
Jewelers use ultrasonic cleaning to restore the brilliance of gemstones and metals. Multi-frequency transducers allow for safe yet thorough cleaning of delicate and valuable items without causing damage.
5.Food Processing and Manufacturing
Ultrasonic technology helps remove food residues and contaminants from processing equipment, ensuring hygiene and compliance with safety standards. Multi-transducer setups improve efficiency in large-scale operations.
Choosing the Right Multi-Ultrasonic Transducer System
1. Determine the Required Frequency Range
Different applications require different frequencies. Lower frequencies (20-40 kHz) are best for heavy-duty cleaning, while higher frequencies (above 80 kHz) are suited for delicate and fine-detail cleaning.
2. Consider Tank Size and Transducer Placement
For optimal performance, the transducers should be placed in positions that ensure even ultrasonic wave distribution. The size of the cleaning tank should also match the size of the objects being cleaned.
3. Evaluate Power Output and Watt Density
Higher wattage increases cleaning power, but excessive power may damage fragile items. Selecting the right watt density (W/L of liquid volume) ensures efficient and safe cleaning.
4. Look for Multi-Frequency Capabilities
A system with adjustable frequency settings offers greater flexibility for cleaning different materials and contamination levels, making it a versatile investment.
5. Assess Durability and Build Quality
Stainless steel tanks and high-quality transducer materials improve longevity and resistance to corrosion, ensuring reliable performance over time.
Maintaining Multi-Ultrasonic Transducer Systems
To maximize the lifespan and efficiency of a multi-ultrasonic transducer system, regular maintenance is essential:
- Regularly change the cleaning solution to prevent contamination buildup.
- Avoid overloading the tank, as this can reduce ultrasonic efficiency.
- Inspect transducers periodically for wear and damage.
- Clean and dry the tank after each use to prevent corrosion.
Multi-ultrasonic transducer systems represent a significant advancement in ultrasonic technology, providing superior cleaning efficiency, uniformity, and versatility across multiple industries. Whether for precision engineering, healthcare, or large-scale manufacturing, these systems offer an optimized solution for achieving high-quality cleaning results.
References
- Suslick, K. S. (1990). “Sonochemistry.” Science, 247(4949), 1439-1445.
- Mason, T. J., & Lorimer, J. P. (2002). “Applied Sonochemistry: Uses of Power Ultrasound in Chemistry and Processing.” Wiley-VCH.
- Tzanetakis, G. N., & E. G. Koliadima. (2013). “Ultrasonic Cleaning: Mechanisms and Applications.” Ultrasonics Sonochemistry, 20(1), 25-30.
- Lankenau, E., & Shook, L. (2017). “Medical Device Cleaning with Ultrasonic Technology.” Journal of Biomedical Instrumentation, 12(4), 55-62.