Ultrasonic transducers are the heart of ultrasonic cleaning machines, converting electrical energy into mechanical vibrations that drive the cleaning process. Among the critical components of these transducers is the vibration plate, a meticulously engineered part that ensures efficient energy transfer and durability. The manufacturing process of ultrasonic transducer groups, particularly the vibration plate, is a fascinating blend of precision engineering, material science, and advanced manufacturing techniques. This article explores the intricate steps involved in creating these essential components, shedding light on the technologies and methodologies that make them possible.
Understanding the Role of the Vibration Plate in Ultrasonic Transducers
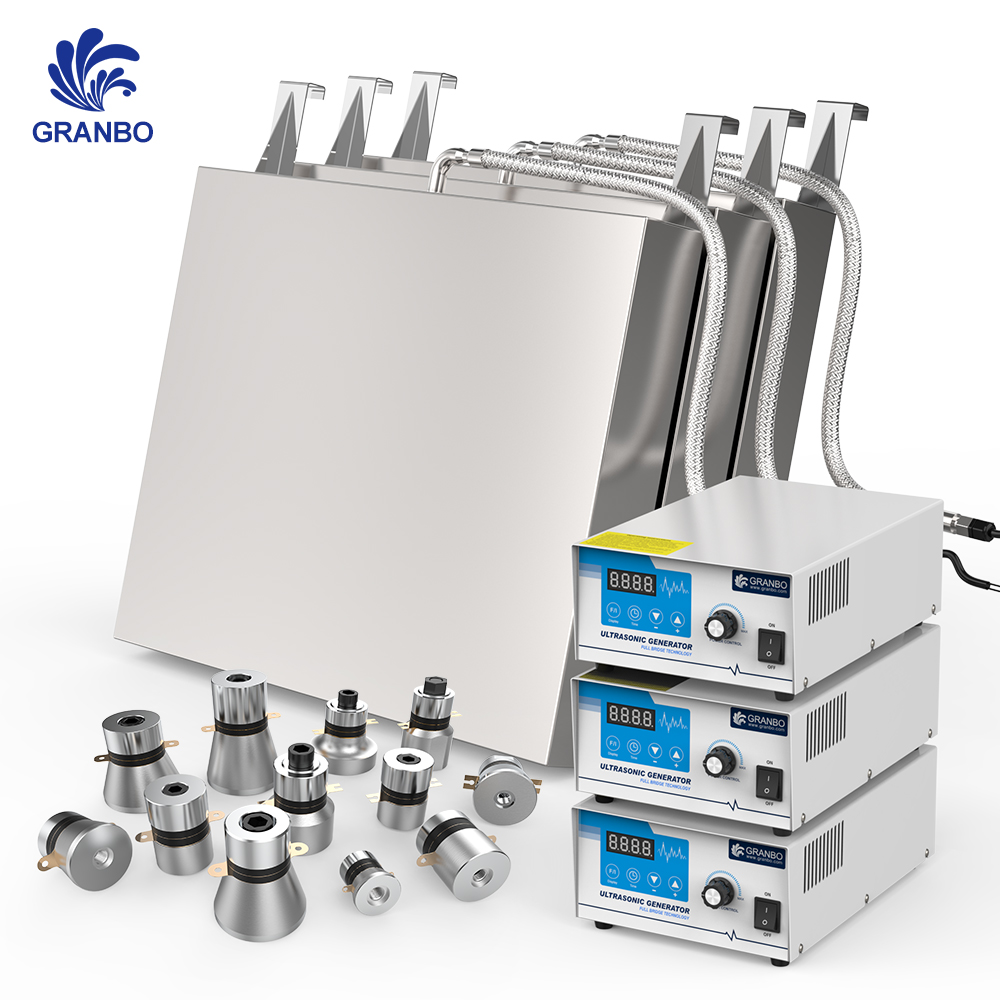
The vibration plate, also known as the diaphragm, is a key element of the ultrasonic transducer group. It is responsible for generating the high-frequency mechanical vibrations that produce cavitation in the cleaning solution. The plate must be designed to withstand repeated stress cycles while maintaining precise vibrational characteristics.
The performance of the vibration plate depends on several factors, including its material composition, thickness, and geometric design. Common materials used for vibration plates include titanium, stainless steel, and aluminum, each chosen for its specific properties such as strength, corrosion resistance, and acoustic impedance.
Material Selection and Preparation
The first step in manufacturing a vibration plate is selecting the appropriate material. The choice of material is critical, as it directly impacts the plate’s durability, efficiency, and compatibility with the transducer’s operating conditions.
1. Titanium: Known for its high strength-to-weight ratio and excellent corrosion resistance, titanium is a popular choice for high-performance vibration plates. It is particularly suitable for applications requiring high frequencies and prolonged use.
2. Stainless Steel: Stainless steel offers a balance of strength, durability, and cost-effectiveness. It is often used in industrial applications where moderate frequencies and robust performance are required.
3. Aluminum: Lightweight and easy to machine, aluminum is ideal for applications where weight reduction is a priority. However, it is less durable than titanium and stainless steel, making it suitable for lower-frequency applications.
Once the material is selected, it undergoes rigorous preparation, including cutting, shaping, and surface treatment. The raw material is typically cut into blanks of the required size and shape using precision machining techniques such as laser cutting or water jet cutting.
Precision Machining and Shaping
The next step in the manufacturing process is precision machining, where the vibration plate is shaped to meet exact specifications. This stage involves several advanced techniques to ensure the plate’s dimensions and surface finish are within tight tolerances.
1. CNC Machining: Computer Numerical Control (CNC) machining is used to create the intricate features of the vibration plate, such as holes, grooves, and mounting points. CNC machines offer high precision and repeatability, ensuring consistent quality across multiple units.
2. Surface Grinding: The surface of the vibration plate is ground to achieve a smooth finish and uniform thickness. This step is crucial for ensuring optimal vibrational performance and minimizing energy losses.
3. Heat Treatment: Depending on the material, the vibration plate may undergo heat treatment to enhance its mechanical properties. For example, titanium plates are often annealed to reduce internal stresses and improve durability.
Assembly of the Transducer Group
Once the vibration plate is machined and prepared, it is assembled into the transducer group. This process involves integrating the plate with other critical components, such as the piezoelectric elements, backing material, and housing.
1. Piezoelectric Elements: These elements are bonded to the vibration plate using specialized adhesives. The bonding process requires precise alignment to ensure uniform energy transfer and optimal performance.
2. Backing Material: A backing material is attached to the rear of the piezoelectric elements to dampen unwanted vibrations and improve the transducer’s efficiency. Common backing materials include epoxy resins and composite materials.
3. Housing: The assembled components are enclosed in a protective housing, which provides mechanical support and shields the transducer from environmental factors such as moisture and dust.
Quality Control and Testing
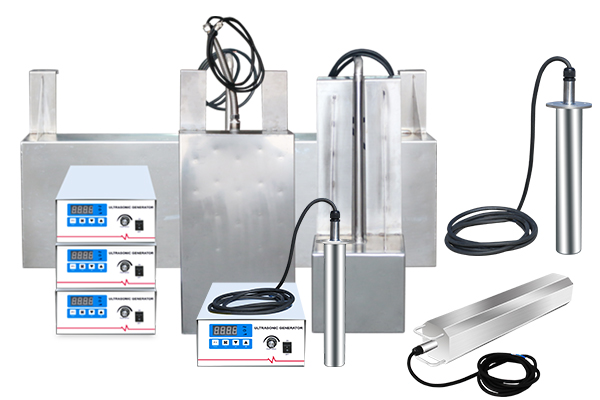
Quality control is a critical aspect of the manufacturing process, ensuring that each vibration plate and transducer group meets stringent performance standards. This stage involves a series of tests and inspections to verify the integrity and functionality of the components.
1. Dimensional Inspection: The vibration plate is measured using precision instruments such as coordinate measuring machines (CMMs) to ensure it conforms to design specifications.
2. Resonance Testing: The transducer group is tested to determine its resonant frequency and vibrational characteristics. This test ensures that the transducer operates efficiently at the desired frequency.
3. Durability Testing: The vibration plate is subjected to stress tests to evaluate its performance under repeated cycles of operation. This step helps identify potential weaknesses and ensures long-term reliability.
4. Acoustic Performance Testing: The transducer group is tested in a simulated cleaning environment to assess its acoustic performance and cavitation efficiency.
Innovations and Future Trends in Vibration Plate Manufacturing
The field of ultrasonic transducer manufacturing is constantly evolving, driven by advancements in materials science, manufacturing technologies, and design methodologies. Emerging trends include the use of additive manufacturing (3D printing) to create complex vibration plate geometries, the development of new composite materials with enhanced properties, and the integration of smart sensors for real-time performance monitoring.
Researchers are also exploring the use of nanotechnology to improve the surface properties of vibration plates, enhancing their resistance to wear and corrosion. These innovations promise to further enhance the efficiency, durability, and versatility of ultrasonic transducers, opening up new possibilities for their application in various industries.
The manufacturing process of ultrasonic transducer groups, particularly the vibration plate, is a testament to the ingenuity and precision of modern engineering. From material selection and precision machining to assembly and quality control, each step is carefully executed to ensure the highest standards of performance and reliability. As technology continues to advance, the future of ultrasonic transducer manufacturing looks brighter than ever, with exciting new developments on the horizon.
References:
1. Berlincourt, D. A., Curran, D. R., & Jaffe, H. (1964). “Piezoelectric and Piezomagnetic Materials and Their Function in Transducers.” Physical Acoustics, 1, 169-270.
2. Uchino, K. (2000). Ferroelectric Devices. CRC Press.
3. Smith, W. A., & Auld, B. A. (1991). “Modeling 1-3 Composite Piezoelectrics: Thickness-Mode Oscillations.” IEEE Transactions on Ultrasonics, Ferroelectrics, and Frequency Control, 38(1), 40-47.
4. IEEE Standard on Piezoelectricity. (1987). ANSI/IEEE Std 176-1987.
5. Mason, W. P. (1948). Electromechanical Transducers and Wave Filters. D. Van Nostrand Company.