Understanding Ultrasonic Cleaning Technology
Ultrasonic cleaning machines have revolutionized the way industries handle delicate and intricate cleaning tasks. These devices use high-frequency sound waves to create microscopic cavitation bubbles that dislodge contaminants from surfaces, making them highly effective for cleaning delicate items such as medical instruments, jewelry, and precision components. But how exactly do these machines work? Understanding their operational mechanism reveals why they are widely used across various industries.
The Role of Cavitation in Ultrasonic Cleaning
At the core of ultrasonic cleaning technology is the process of cavitation. When ultrasonic waves pass through a liquid medium, they create rapid pressure changes, forming tiny vacuum bubbles. These bubbles expand and collapse with immense force, generating localized high temperatures and pressures that effectively remove dirt, grease, and other unwanted particles from surfaces. The implosion of these bubbles produces microjets of liquid, which further enhance the cleaning process by penetrating even the smallest crevices and blind holes of objects being cleaned.
Cavitation occurs due to the alternating high- and low-pressure cycles induced by ultrasonic waves. The frequency of these waves, typically ranging from 20 kHz to 400 kHz, determines the cleaning intensity. Lower frequencies create larger cavitation bubbles that exert more force, suitable for heavy-duty cleaning, whereas higher frequencies generate finer bubbles, ideal for delicate materials.
Key Components of an Ultrasonic Cleaning Machine
To better grasp the working mechanism, it’s essential to understand the main components of an ultrasonic cleaner:
- Ultrasonic Transducers – These devices convert electrical energy into ultrasonic sound waves. They are typically piezoelectric or magnetostrictive, with piezoelectric transducers being the most common due to their efficiency and reliability.
- Generator – The generator powers the transducers by supplying high-frequency electrical energy. It controls the frequency and intensity of the ultrasonic waves, allowing for adjustable cleaning settings.
- Cleaning Tank – The tank holds the cleaning solution and the items being cleaned. It is usually made of stainless steel to withstand cavitation effects and corrosion.
- Cleaning Solution – The type of liquid used plays a crucial role in the cleaning process. Water-based solutions with added detergents or specialized solvents enhance cleaning efficiency by breaking down contaminants chemically while cavitation removes them physically.
- Heater and Timer – Some ultrasonic cleaners are equipped with heaters to optimize cleaning performance, as certain contaminants dissolve better at higher temperatures. Timers allow users to set specific cleaning durations for different applications.
Factors Affecting the Efficiency of Ultrasonic Cleaning
Several factors influence how effectively an ultrasonic cleaner removes contaminants:
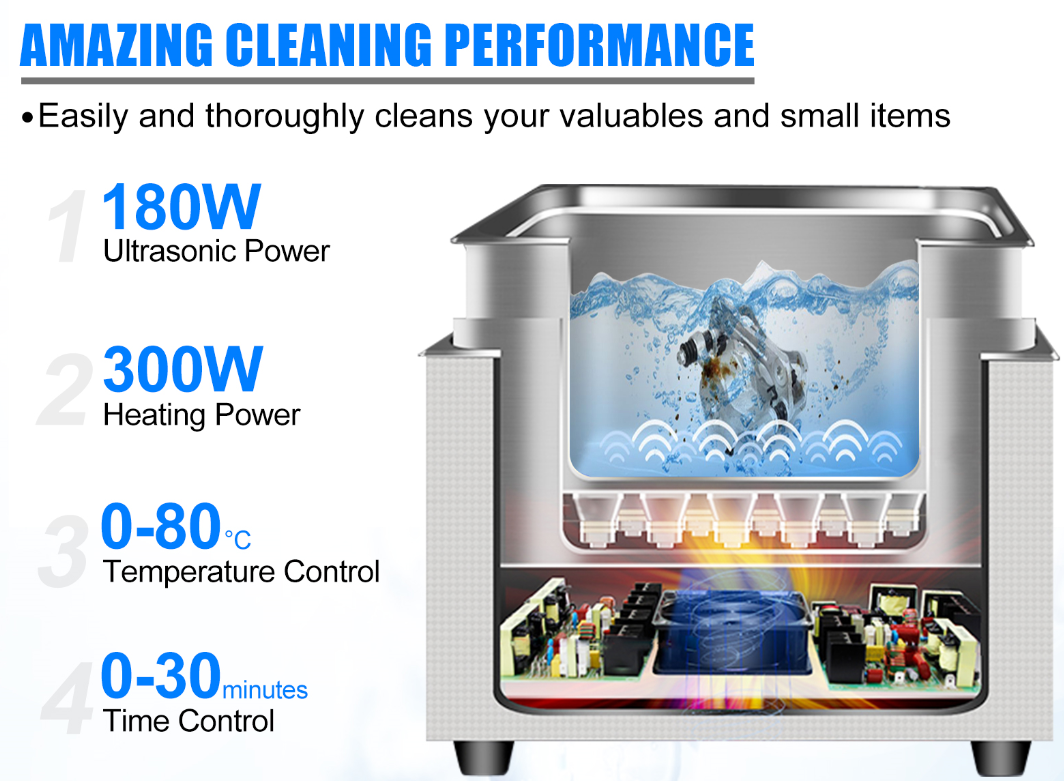
- Frequency: Different applications require specific frequencies. For example, 25-40 kHz is suitable for general cleaning, while 80-130 kHz is preferred for delicate objects like microelectronics.
- Temperature: Higher temperatures (usually between 40°C and 60°C) improve cleaning efficiency by reducing the viscosity of the cleaning solution and enhancing cavitation.
- Cleaning Solution: The choice of solvent or detergent significantly impacts the results. Alkaline solutions work well for degreasing, while acidic solutions are effective for removing oxides.
- Cleaning Time: Longer exposure allows more thorough cleaning, but excessive durations may damage sensitive items.
- Object Placement: Items should be fully submerged and positioned correctly within the tank to ensure even cleaning.
Applications of Ultrasonic Cleaning Machines
The versatility of ultrasonic cleaning machines makes them indispensable across various industries:
- Medical and Dental: Used for sterilizing surgical tools and dental instruments by eliminating microscopic contaminants.
- Jewelry and Watches: Restores shine to delicate pieces without causing mechanical damage.
- Automotive and Aerospace: Cleans fuel injectors, carburetors, and other precision parts.
- Electronics: Removes flux residues from circuit boards without harming sensitive components.
- Manufacturing and Industrial: Ensures precision cleaning of machined parts, molds, and other intricate equipment.
Enhancements and Future Trends in Ultrasonic Cleaning
Advancements in ultrasonic cleaning technology continue to push efficiency and effectiveness. Innovations such as multi-frequency systems allow for customized cleaning approaches, while automated systems integrate ultrasonic cleaners into production lines for streamlined operations. Additionally, eco-friendly cleaning solutions are becoming more prevalent, reducing the reliance on harsh chemicals while maintaining cleaning efficacy.
With industries demanding increasingly precise cleaning solutions, the development of next-generation ultrasonic cleaning machines focuses on improving energy efficiency, reducing noise levels, and enhancing adaptability for diverse applications. As research continues, we can expect further refinements in transducer technology, better material compatibility, and smarter control interfaces to enhance user experience and effectiveness.
References
- Suslick, K. S. (1990). Sonochemistry. Science, 247(4949), 1439-1445.
- Mason, T. J. (2011). Sonochemistry and Sonoluminescence: Advances in Ultrasonic Cleaning. CRC Press.
- Nyborg, W. L. (2001). Ultrasonic Cleaning Mechanisms. Ultrasonics, 39(2), 159-172.
- Ashokkumar, M. (2016). The Science and Engineering of Ultrasonic Cavitation. Ultrasonics Sonochemistry, 32, 30-35.
This comprehensive guide offers valuable insights into the operational mechanism of ultrasonic cleaning machines, shedding light on why they remain a preferred choice for high-precision cleaning across diverse fields.