The Role of Ultrasonic Transducer Arrays in Modern Applications
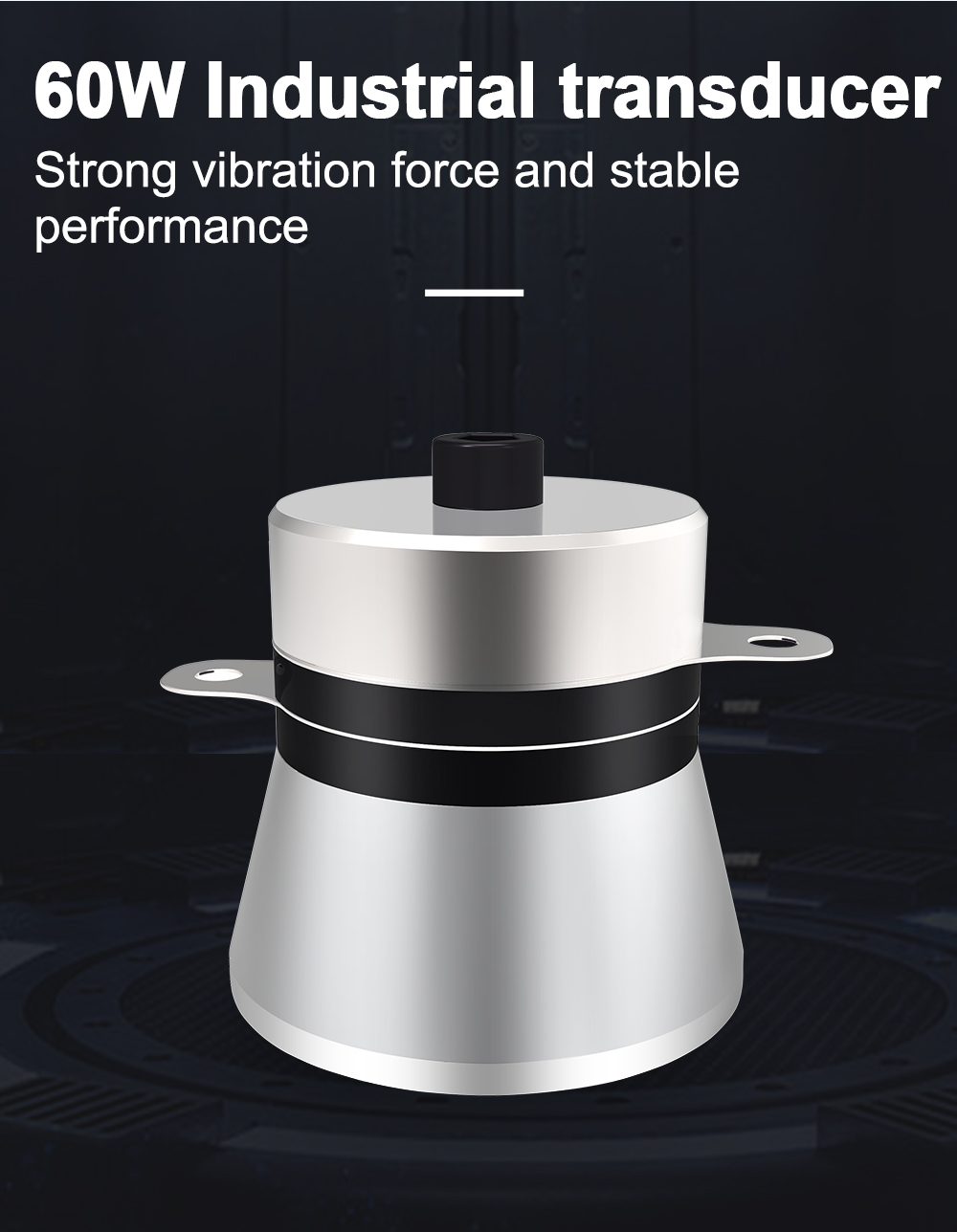
Ultrasonic transducer arrays, commonly integrated into vibration plates, play a crucial role in various industries, including medical imaging, industrial cleaning, and underwater sonar systems. These arrays convert electrical energy into high-frequency mechanical vibrations, enabling precise and efficient ultrasonic applications. The effectiveness of an ultrasonic transducer array is largely dependent on its manufacturing process, which involves precision engineering and advanced material selection.
Producing a high-performance ultrasonic transducer array requires careful consideration of factors such as piezoelectric material properties, bonding techniques, electrode design, and housing construction. By optimizing the manufacturing process, industries can enhance efficiency, durability, and overall performance.
Material Selection for Ultrasonic Transducer Arrays
The choice of materials is fundamental to the functionality and longevity of ultrasonic transducers. Key components include:
- Piezoelectric Materials: The heart of an ultrasonic transducer is the piezoelectric element, which generates vibrations when subjected to an electric field. Common materials include:
- Lead Zirconate Titanate (PZT): Offers high efficiency and strong piezoelectric properties.
- Lithium Niobate (LiNbO3): Used in applications requiring high-frequency stability.
- Quartz: Provides lower performance but excellent thermal stability.
- Electrodes and Conductive Layers: The electrodes facilitate the transmission of electrical signals to the piezoelectric material. These are typically made from:
- Silver (Ag) or Silver-Palladium (Ag-Pd) alloys for high conductivity.
- Gold (Au) coatings for specialized applications requiring superior corrosion resistance.
- Backing and Damping Materials: To optimize signal transmission and reduce unwanted vibrations, backing layers made from epoxy resins, tungsten, or polymer composites are used.
- Casing and Housing: Stainless steel, aluminum, or polymer enclosures provide protection against environmental factors such as moisture and mechanical stress.
The combination of these materials must be carefully selected to achieve the best trade-off between performance, durability, and cost.
Precision Manufacturing Process of Ultrasonic Transducer Arrays
The production of ultrasonic transducer arrays involves several critical steps, each requiring meticulous precision and quality control. The key stages include:
1. Preparation of Piezoelectric Elements
The manufacturing process begins with the preparation of the piezoelectric material. This involves:
- Cutting bulk piezoelectric ceramics into precisely sized elements using laser cutting or diamond saws.
- Polishing the surfaces to ensure uniformity and optimal contact with electrodes.
- Applying polarization treatment by exposing the material to a strong electric field to enhance its piezoelectric properties.
2. Electrode Deposition
After polarization, thin metallic electrode layers are deposited onto the piezoelectric material. This step typically involves:
- Physical Vapor Deposition (PVD): A vacuum-based process that ensures uniform metal coating.
- Screen Printing: Used for cost-effective large-scale production of electrodes.
- Electroplating: Enhances conductivity and adhesion of electrode layers.
The precision of electrode placement directly impacts the transducer’s efficiency and signal transmission capabilities.
3. Array Assembly and Bonding
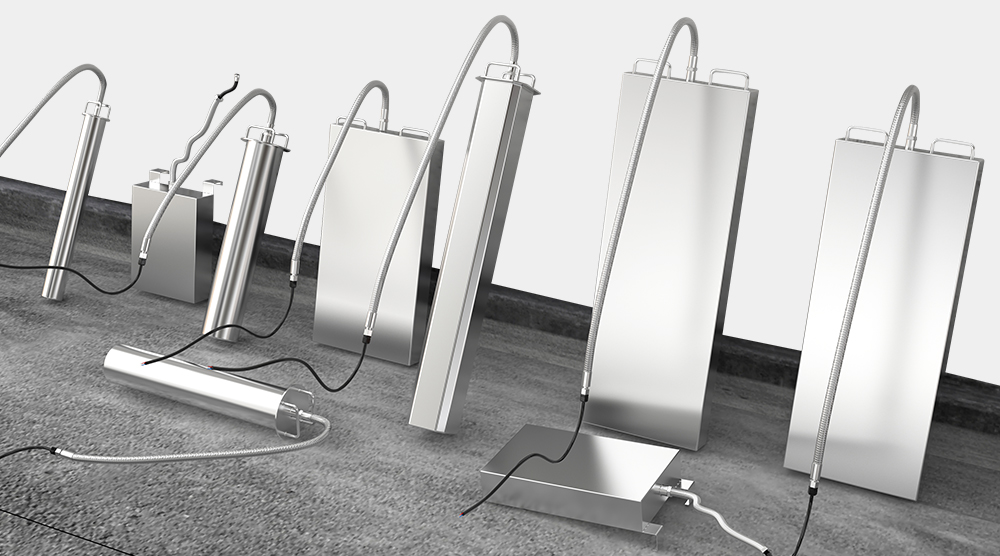
Once individual transducer elements are prepared, they are arranged into an array and bonded to a common substrate. This step involves:
- Adhesive Bonding: Using epoxy or polymer adhesives for secure attachment.
- Soldering or Ultrasonic Welding: Ensures robust electrical connections.
- Laminating Multiple Layers: For advanced multi-frequency or broadband transducers.
Alignment precision is crucial to maintain uniform vibration patterns across the array, enhancing performance in applications such as ultrasonic imaging and material testing.
Testing and Quality Control in Transducer Manufacturing
To ensure the reliability and performance of ultrasonic transducer arrays, rigorous testing and quality control measures are implemented. Key testing procedures include:
- Resonance Frequency Testing: Confirms that the transducer operates at the desired ultrasonic frequency.
- Impedance Analysis: Measures electrical impedance to detect material inconsistencies or bonding defects.
- Acoustic Power Output Testing: Evaluates the efficiency of ultrasound transmission and vibration strength.
- Environmental Stress Testing: Subjects transducers to temperature variations, humidity, and mechanical stress to ensure durability in real-world applications.
High-precision instruments such as network analyzers, laser vibrometers, and hydrophones are used to conduct these tests, ensuring compliance with industry standards.
Future Innovations in Ultrasonic Transducer Array Manufacturing
With rapid advancements in materials science and manufacturing technologies, the production of ultrasonic transducer arrays is evolving. Some emerging trends include:
- 3D Printing of Piezoelectric Materials: Enables more complex transducer geometries and customization for specific applications.
- Flexible and Wearable Ultrasonic Transducers: Development of bendable transducer arrays for medical diagnostics and soft robotics.
- Nanostructured Electrodes: Enhancing signal transmission efficiency and reducing energy losses.
- AI-Driven Manufacturing Optimization: Utilizing machine learning algorithms to predict and correct defects during production.
As these technologies continue to develop, ultrasonic transducers will become more efficient, cost-effective, and versatile, expanding their applications across multiple industries.
References
- Ballato, A. (2019). Piezoelectric Transducers and Applications. Springer.
- Smith, W. A. & Auld, B. A. (2020). Ultrasonic Transducer Materials and Design Considerations. IEEE Transactions on Ultrasonics.
- Haertling, G. H. (2018). Ferroelectric Ceramics: History and New Developments. Journal of the American Ceramic Society.
- Current industry reports and research articles from ScienceDirect and IEEE Xplore on ultrasonic transducer manufacturing.