The Role of Cleaning Solutions in Ultrasonic Cleaning
Ultrasonic cleaning has revolutionized industries that require precision cleaning, such as medical, automotive, and electronics manufacturing. The efficiency of an ultrasonic cleaning system depends on multiple factors, with the cleaning solution playing a crucial role. The right formulation of the cleaning liquid enhances cavitation, removes contaminants effectively, and prevents surface damage. A well-optimized solution not only improves cleaning efficiency but also extends the lifespan of both the ultrasonic machine and the components being cleaned.
Composition and Types of Ultrasonic Cleaning Solutions
Selecting the appropriate cleaning solution is essential for maximizing ultrasonic cleaning performance. These solutions generally fall into three main categories:
1. Aqueous Solutions
Aqueous-based cleaning solutions are water-based formulations that often contain surfactants, detergents, or enzymes to enhance cleaning performance. They are widely used for applications where mild yet effective cleaning is required, such as in medical instruments and delicate electronic components.
- Alkaline Solutions: Used for removing oils, grease, and organic contaminants.
- Acidic Solutions: Effective for removing rust, scale, and mineral deposits but must be handled carefully.
- Neutral Solutions: Suitable for sensitive materials, such as jewelry and optical lenses.
2. Solvent-Based Solutions
Solvent-based solutions are designed for applications requiring powerful degreasing or removal of contaminants that are insoluble in water. Common solvents include hydrocarbons, alcohols, and halogenated compounds. These solutions are typically used in industrial and aerospace applications where high precision cleaning is needed.
3. Specialty Solutions
Specialized formulations cater to unique cleaning needs, such as enzymatic solutions for medical and dental applications, or biodegradable solutions designed for environmentally friendly cleaning processes.
Key Parameters for Ultrasonic Cleaning Optimization
Optimizing ultrasonic cleaning requires careful control of various operational parameters. These factors determine the effectiveness of cavitation and the overall success of the cleaning process.
1. Frequency Selection
Ultrasonic frequency directly influences cavitation intensity and bubble size, which affects the cleaning performance.
- Low Frequencies (20-40 kHz): Generate large cavitation bubbles, suitable for removing heavy contaminants from durable surfaces.
- Mid-Range Frequencies (40-80 kHz): Ideal for general cleaning applications, such as medical instruments and automotive components.
- High Frequencies (80-200 kHz): Create smaller bubbles, making them perfect for delicate cleaning applications like semiconductor wafers and precision optics.
2. Power and Intensity Control
The power of an ultrasonic cleaner, measured in watts per liter, determines the intensity of cavitation. Higher power levels enhance cleaning efficiency but can also cause damage to fragile materials. Proper calibration is necessary to balance power and safety.
3. Temperature Regulation
The temperature of the cleaning solution plays a crucial role in ultrasonic cleaning. Heating the solution enhances the effectiveness of detergents, improves cavitation efficiency, and helps dissolve stubborn contaminants. Common temperature ranges include:
- Room Temperature to 40°C: Suitable for delicate items such as electronic components and jewelry.
- 40°C to 60°C: Enhances the removal of oils and grease from mechanical parts.
- Above 60°C: Used for heavy-duty industrial cleaning, but excessive heat may reduce cavitation efficiency.
4. Cleaning Cycle Duration
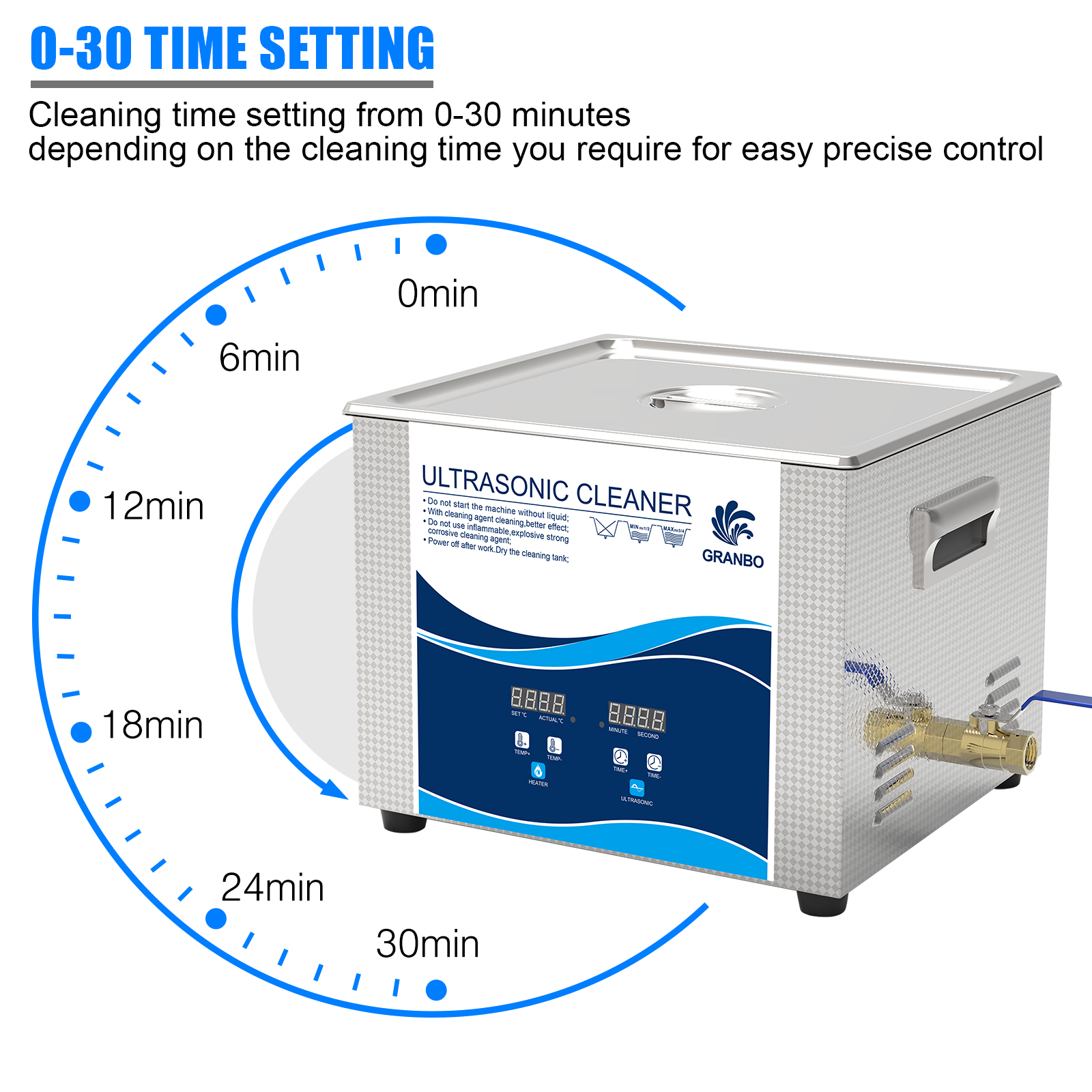
The duration of ultrasonic cleaning cycles depends on the type and level of contamination. Shorter cycles are sufficient for light cleaning, while heavily soiled components require extended cleaning times. Typical cycles range from 3 to 20 minutes, with some industrial applications requiring up to an hour.
5. Solution Degassing
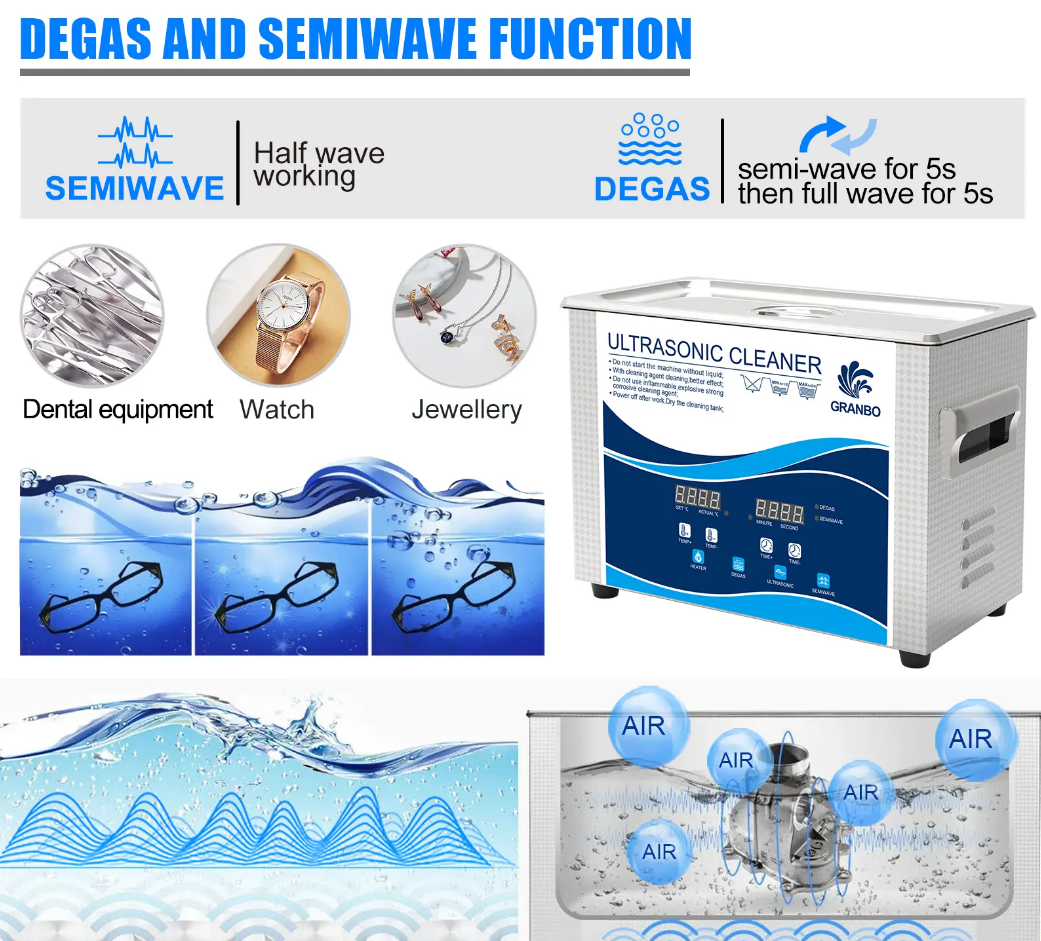
Dissolved gases in the cleaning solution can hinder cavitation efficiency. Degassing the solution before operation improves performance by eliminating air bubbles that absorb ultrasonic energy. Many modern ultrasonic cleaning machines include automatic degassing functions to optimize cleaning effectiveness.
Advancements in Ultrasonic Cleaning Technology
The ultrasonic cleaning industry continues to evolve, incorporating new technologies to improve efficiency and sustainability. Some emerging trends include:
- Smart Ultrasonic Cleaners: Integration of IoT and AI for automated monitoring and process optimization.
- Eco-Friendly Solutions: Development of biodegradable and non-toxic cleaning solutions to reduce environmental impact.
- Multi-Frequency Systems: Machines with adjustable frequency settings to accommodate different cleaning needs within a single unit.
- Nanotechnology Applications: Use of nano-enhanced cleaning fluids for superior contaminant removal at the microscopic level.
Ultrasonic cleaning remains an indispensable technology across industries, driven by continuous innovation in cleaning solutions and parameter optimization. By understanding the interplay between ultrasonic frequency, power, temperature, and cleaning agents, users can achieve superior cleaning results while prolonging the lifespan of their equipment.
References
- Mason, T. J., & Peters, D. (2002). Practical Sonochemistry: Uses and Applications of Ultrasound. Ellis Horwood Limited.
- Ensminger, D., & Bond, L. J. (2011). Ultrasonics: Fundamentals, Technologies, and Applications. CRC Press.
- Gogate, P. R., & Pandit, A. B. (2011). A review of imperative technologies for wastewater treatment II: Hybrid methods. Advances in Environmental Research, 15(1), 1-20.
- Leighton, T. G. (1994). The Acoustic Bubble. Academic Press.
- Krefting, D., & Giese, U. (2019). Development of efficient ultrasonic cleaning systems for industrial applications. Journal of Ultrasonic Technology, 35(3), 215-228.