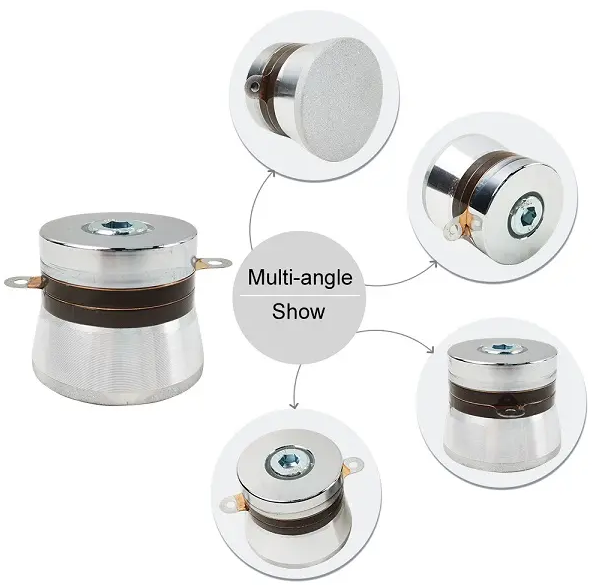
Ultrasonic generators are the backbone of modern industrial cleaning, welding, and precision machining processes. These devices convert electrical energy into high-frequency sound waves, enabling the removal of contaminants, bonding of materials, and even medical imaging. However, the efficiency and reliability of ultrasonic generators depend heavily on proper matching and debugging. Without these critical steps, even the most advanced equipment can underperform or fail prematurely. This article explores the intricacies of matching and debugging ultrasonic generators, offering insights into best practices, common challenges, and innovative solutions.
Understanding Ultrasonic Generators: The Basics
Ultrasonic generators are electronic devices that produce high-frequency electrical signals, typically ranging from 20 kHz to several megahertz. These signals drive ultrasonic transducers, which convert the electrical energy into mechanical vibrations. The vibrations are then used for various applications, such as cleaning delicate components, welding plastics, or emulsifying liquids.
The performance of an ultrasonic generator depends on its ability to match the impedance of the transducer and maintain stable frequency output. Mismatched systems can lead to energy loss, overheating, and even damage to the equipment. For example, a generator designed for a 40 kHz transducer may not perform optimally with a 25 kHz transducer due to differences in impedance and resonance characteristics.
The Importance of Impedance Matching
Impedance matching is a critical aspect of ultrasonic generator performance. It ensures that the maximum amount of electrical energy is transferred from the generator to the transducer, minimizing losses and maximizing efficiency. When the impedance of the generator and transducer are mismatched, a significant portion of the energy is reflected back into the generator, leading to inefficiency and potential damage.
To achieve optimal impedance matching, engineers often use matching networks, which consist of inductors and capacitors. These components adjust the electrical characteristics of the system to ensure compatibility between the generator and transducer. For instance, the SONIC DIGITAL MG SINGLE BASIC generator from Weber Ultrasonics features advanced impedance matching capabilities, allowing it to operate efficiently across a wide range of frequencies and power levels.
Debugging Ultrasonic Generators: Common Challenges and Solutions
Debugging ultrasonic generators involves identifying and resolving issues that affect their performance. Common challenges include frequency drift, power instability, and overheating.
1. Frequency Drift: Frequency drift occurs when the generator’s output frequency deviates from the desired value. This can be caused by temperature fluctuations, aging components, or improper tuning. To address this issue, modern generators like the SONOPOWER 3S series use digital frequency control systems that automatically adjust the output frequency to maintain stability.
2. Power Instability: Power instability can result from impedance mismatches or faulty components. For example, if the transducer’s impedance changes due to wear or contamination, the generator may struggle to deliver consistent power. Regular maintenance and calibration can help mitigate this issue.
3. Overheating: Overheating is often caused by excessive energy reflection or poor ventilation. Generators with built-in temperature management systems, such as the Sonic Digital MG Single Basic, can detect and prevent overheating by adjusting the power output or activating cooling fans.
Advanced Techniques for Matching and Debugging
As ultrasonic technology continues to evolve, so do the techniques for matching and debugging generators. Some of the most innovative approaches include:
1. Automated Matching Systems: These systems use algorithms to analyze the impedance of the transducer and adjust the generator’s output in real time. This eliminates the need for manual tuning and ensures optimal performance under varying conditions.
2. Digital Signal Processing (DSP): DSP technology allows generators to monitor and adjust their output signals with high precision. For example, the SONOPOWER 3S DUAL generator uses DSP to create stable and efficient ultrasonic waves, even in demanding industrial environments.
3. Predictive Maintenance: By analyzing data from sensors and monitoring systems, engineers can predict when a generator is likely to fail and take preventive action. This reduces downtime and extends the lifespan of the equipment.
Case Studies: Real-World Applications
To illustrate the importance of matching and debugging, let’s examine two real-world applications:
1. Industrial Cleaning: In a manufacturing facility, an ultrasonic cleaning system was experiencing frequent breakdowns due to mismatched generators and transducers. After implementing an automated matching system and conducting regular debugging, the facility achieved a 30% increase in efficiency and a 50% reduction in downtime.
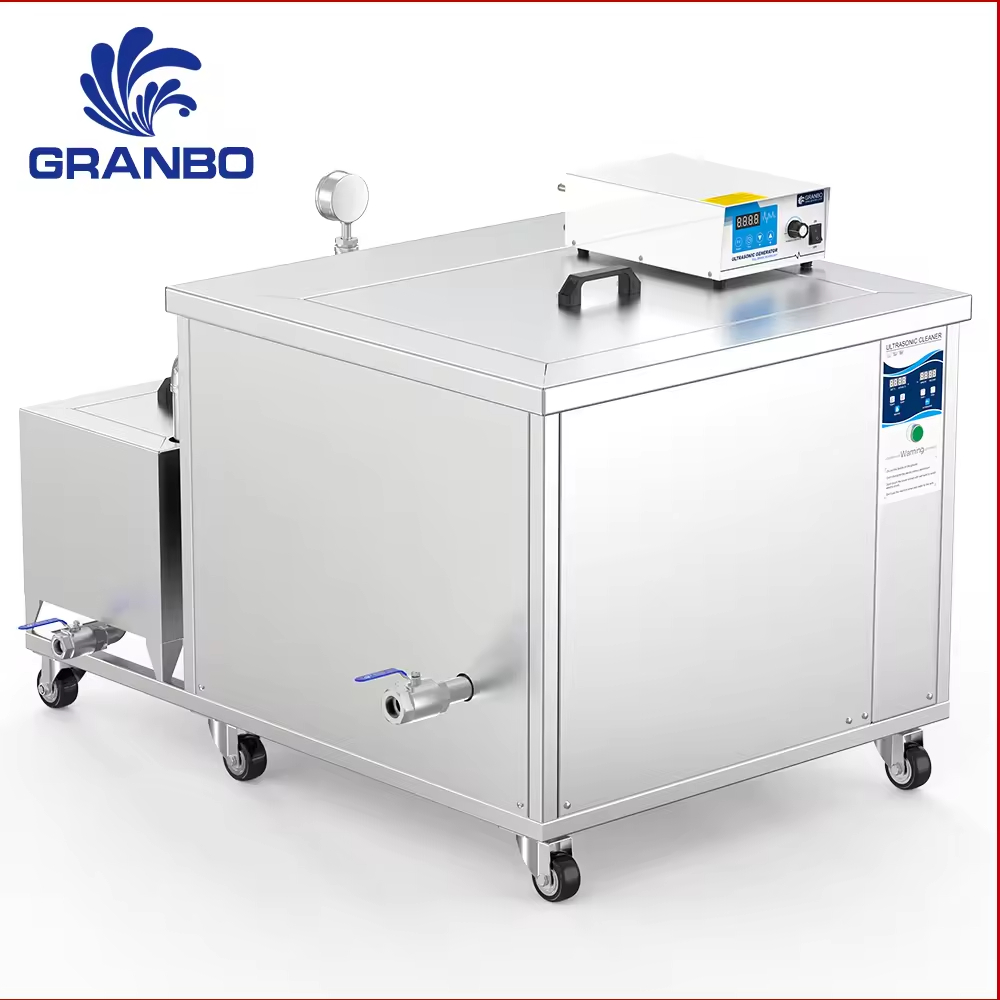
2. Medical Device Manufacturing: A medical device manufacturer was struggling with inconsistent welding results. By upgrading to a generator with advanced DSP capabilities and optimizing the impedance matching, the company improved product quality and reduced waste by 20%.
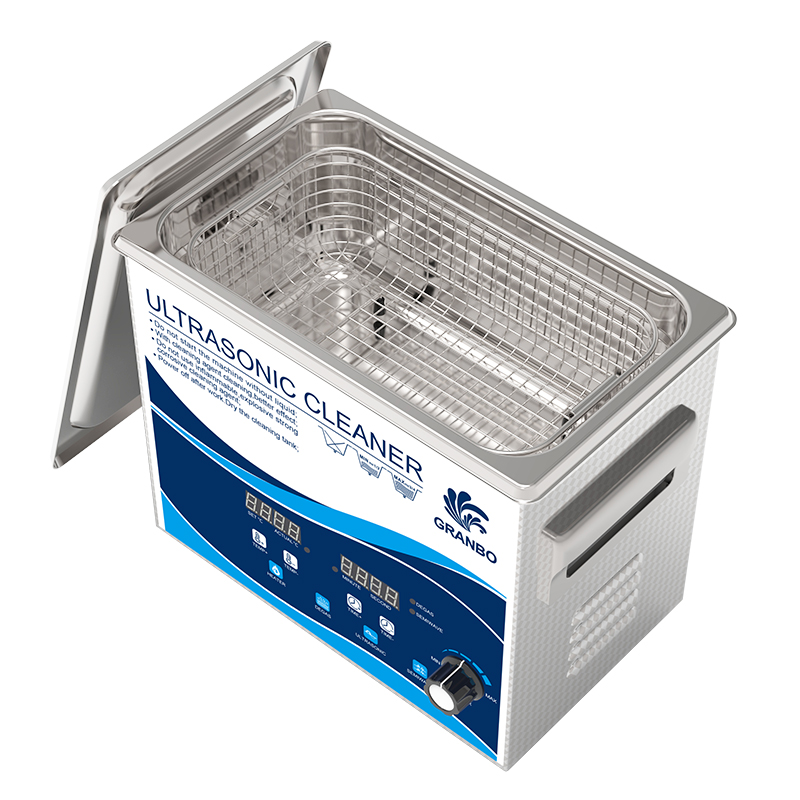
Future Trends in Ultrasonic Generator Technology
The future of ultrasonic generators lies in smarter, more efficient, and more versatile designs. Emerging trends include:
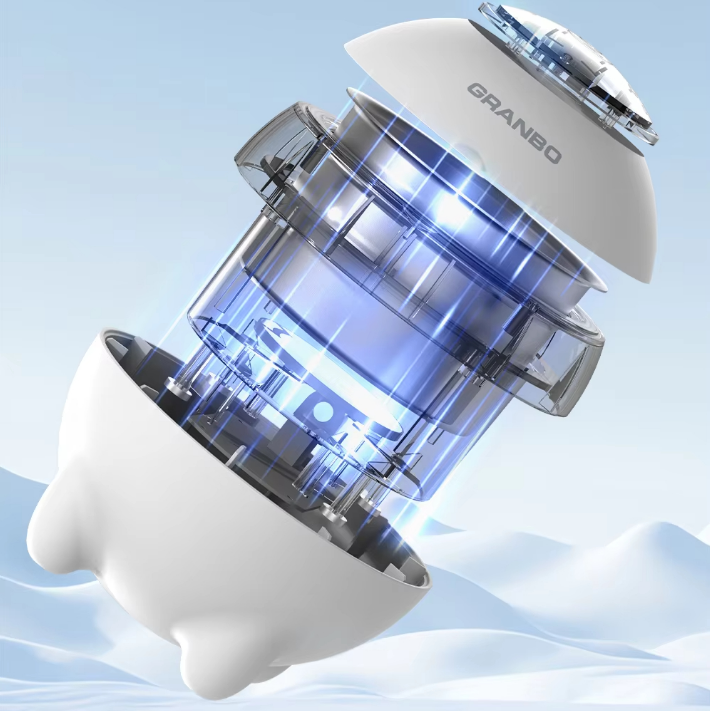
1. Integration with IoT: Ultrasonic generators equipped with IoT capabilities can communicate with other devices and systems, enabling remote monitoring and control.
2. Energy-Efficient Designs: As sustainability becomes a priority, manufacturers are developing generators that consume less energy while delivering the same or better performance.
3. Miniaturization: Advances in microelectronics are making it possible to create smaller, more compact ultrasonic generators for use in portable and handheld devices.
By understanding the principles of matching and debugging, engineers and technicians can unlock the full potential of ultrasonic generators. Whether in industrial cleaning, medical device manufacturing, or precision machining, these devices play a vital role in modern technology. With the right knowledge and tools, we can ensure they continue to perform at their best, driving innovation and efficiency across industries.
References
1. DirectIndustry. (2022). *Ultrasonic generator – All industrial manufacturers*. Retrieved from [http://www.directindustry.com](http://www.directindustry.com).
2. The Free Dictionary. (2025). *Ultrasonic generator – definition of ultrasonic generator by The Free Dictionary*. Retrieved from [http://www.thefreedictionary.com](http://www.thefreedictionary.com).
3. Made-in-China. (2024). *Ultrasonic Generator – Ultrasonic Generator and Ultrasonic Power Supply*. Retrieved from [https://www.made-in-china.com](https://www.made-in-china.com).
4. Weber Ultrasonics. (2024). *Cleaning ultrasonic generator SONIC DIGITAL MG SINGLE BASIC*. Retrieved from [https://www.directindustry.com](https://www.directindustry.com).