Understanding the Core Principles of Ultrasonic Cleaning
Ultrasonic cleaning technology has become an essential tool in various industries, offering a highly efficient method for removing contaminants from complex and delicate surfaces. By utilizing high-frequency sound waves, this process generates microscopic cavitation bubbles that effectively dislodge dirt, grease, and other residues. While the basic mechanism remains consistent, several design elements play a crucial role in optimizing the cleaning performance. The effectiveness of an ultrasonic cleaning system depends on multiple factors, including frequency selection, transducer placement, tank design, cleaning solutions, and temperature control. Carefully considering these elements ensures maximum efficiency and longevity of the equipment.
Key Design Factors That Influence Ultrasonic Cleaning Performance
1. Frequency Selection: Matching the Right Frequency to the Cleaning Task
The frequency of ultrasonic waves is a fundamental aspect that dictates the cleaning intensity. Typical ultrasonic cleaning systems operate within a range of 20 kHz to 200 kHz, with different applications requiring specific frequencies:
- Low-frequency (20-40 kHz): Suitable for heavy-duty cleaning tasks involving large, durable components such as engine parts and industrial tools. This range generates larger cavitation bubbles, providing strong cleaning power but with a higher risk of surface erosion.
- Medium-frequency (40-80 kHz): Ideal for general-purpose cleaning, such as medical instruments, automotive parts, and precision tools. It balances cleaning intensity and surface protection.
- High-frequency (80-200 kHz): Recommended for delicate components like microelectronics, optical lenses, and fine jewelry. Higher frequencies create smaller cavitation bubbles, ensuring a gentle cleaning process without damaging sensitive materials.
Selecting the right frequency is essential to achieving optimal cleaning efficiency while preserving the integrity of the items being cleaned.
2. Transducer Placement and Configuration
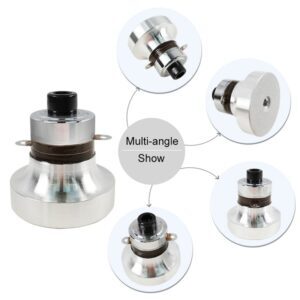
Transducers are responsible for converting electrical energy into ultrasonic waves. Their placement and configuration significantly affect the uniformity and effectiveness of the cleaning process. Two primary types of transducers are used in ultrasonic cleaning systems:
- Bonded transducers: Fixed to the bottom or sides of the cleaning tank, these transducers offer a direct and stable ultrasonic wave transmission.
- Immersible transducers: Installed as separate units that can be placed in various tank positions, providing flexibility in wave distribution.
Proper transducer arrangement ensures even cavitation throughout the cleaning tank, preventing dead zones where cleaning effectiveness is reduced. Multi-transducer setups, including side and bottom placements, are often used for high-precision applications where uniform cleaning is critical.
3. Tank Design and Material Considerations
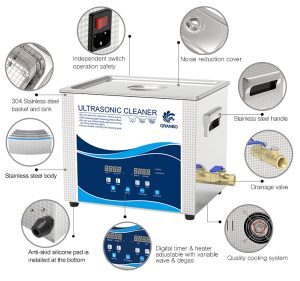
The cleaning tank is a core component of any ultrasonic cleaning system, influencing both performance and durability. Several factors must be considered when designing an ultrasonic cleaning tank:
- Material: Stainless steel is the preferred choice due to its corrosion resistance and ability to withstand prolonged exposure to cleaning solutions and ultrasonic vibrations.
- Tank size: The dimensions should be appropriate for the largest items being cleaned, with enough space to allow efficient cavitation while minimizing solution waste.
- Tank shape: Rectangular tanks are commonly used, but specialized shapes may be necessary for unique cleaning applications.
- Wall thickness: Adequate thickness ensures durability while allowing effective transmission of ultrasonic waves without excessive energy loss.
A well-designed tank contributes to efficient energy utilization and extends the lifespan of the ultrasonic cleaning system.
4. Cleaning Solution Selection and Its Role in Performance
While ultrasonic waves provide mechanical action for cleaning, the choice of cleaning solution significantly impacts overall effectiveness. Different types of contaminants require specific solutions to enhance cleaning performance:
- Aqueous solutions: Water-based detergents are widely used due to their environmental friendliness and ability to remove oils, grease, and particulates.
- Solvent-based solutions: These solutions are effective for degreasing and removing stubborn residues but require careful handling due to potential safety and environmental concerns.
- Enzymatic cleaners: Commonly used in medical and laboratory applications, these solutions break down organic residues like blood and proteins without damaging delicate instruments.
- Alkaline and acidic solutions: Alkaline cleaners are effective for removing oils and carbon deposits, while acidic solutions are used for descaling and rust removal.
The correct cleaning solution enhances cavitation efficiency, ensuring contaminants are removed thoroughly while protecting the integrity of the cleaned objects.
5. Temperature Control and Its Impact on Cleaning Efficiency
Temperature plays a critical role in ultrasonic cleaning by enhancing cavitation and accelerating the breakdown of contaminants. However, excessive heat can negatively impact sensitive materials. Key considerations include:
- Optimal temperature range: Most ultrasonic cleaning processes operate effectively between 40°C and 60°C (104°F – 140°F). Higher temperatures improve the breakdown of oils and greases but may degrade delicate materials.
- Solution compatibility: Certain cleaning solutions work best at specific temperatures, and exceeding recommended limits may reduce their effectiveness or cause unwanted chemical reactions.
- Heat distribution: Ensuring even heating throughout the cleaning tank prevents inconsistent results, which can be achieved with built-in heating elements and thermostatic control.
Proper temperature regulation optimizes cleaning performance while preserving the longevity of the cleaning solution and the items being processed.
Enhancing Efficiency with Advanced Ultrasonic Cleaning Features
Modern ultrasonic cleaning systems come equipped with additional features that improve usability, efficiency, and precision. Some of these enhancements include:
- Degassing functions: Removing trapped air from the cleaning solution enhances cavitation performance, particularly for newly prepared solutions.
- Sweep mode technology: This feature prevents standing waves by varying frequency slightly, ensuring more uniform cleaning across the entire tank.
- Filtration systems: Continuous filtration helps maintain the cleaning solution’s effectiveness by removing contaminants as they are dislodged.
- Programmable timers and automation: Advanced systems allow users to set specific cleaning cycles, improving consistency and reducing manual intervention.
Incorporating these features into an ultrasonic cleaning system can significantly improve results and operational efficiency.
Making the Right Choice for Your Ultrasonic Cleaning Needs
Selecting and designing an ultrasonic cleaning process requires careful evaluation of frequency, transducer configuration, tank specifications, cleaning solutions, and temperature control. Each element contributes to the overall effectiveness of the cleaning process, ensuring that contaminants are removed efficiently while maintaining the integrity of the cleaned items.
By understanding and optimizing these design elements, industries ranging from healthcare to manufacturing can benefit from a reliable and effective ultrasonic cleaning system tailored to their specific needs.
References
- Suslick, K. S. (1990). “Sonochemistry and Ultrasonic Cleaning: The Mechanisms of Cavitation.” Science, 247(4949), 1439-1445.
- Rooney, J. A. (1970). “Ultrasonic Cleaning Technology and Its Industrial Applications.” Journal of Applied Physics, 41(5), 2305-2310.
- Mason, T. J. (2011). “Advances in Ultrasonic Cleaning Design and Performance.” Ultrasonics Sonochemistry, 18(4), 872-880.
- Koda, S., Kimura, T., & Mitome, H. (2003). “Cavitation Science and Ultrasonic Cleaning Optimization.” Ultrasonics, 41(4), 329-336.