Ultrasonic cleaning has revolutionized industries by offering an efficient, reliable, and non-damaging method of cleaning delicate parts and components. The technology uses high-frequency sound waves to generate microscopic bubbles in a cleaning solution, which implode and release energy to remove contaminants. This process, known as cavitation, is widely employed in various sectors, such as automotive, healthcare, electronics, and jewelry manufacturing.
The versatility of ultrasonic cleaning instruments has led to the development of various types designed for different applications. In this article, we’ll explore the different classifications of ultrasonic cleaning instruments, their features, and the specific roles they play in various industries.
1. General Overview of Ultrasonic Cleaning Technology
Before delving into the specific types of ultrasonic cleaning instruments, it’s important to understand the core technology behind them. Ultrasonic cleaning works by generating high-frequency sound waves (typically between 20 kHz and 2 MHz) that create rapid pressure changes in a liquid medium. These pressure waves generate microscopic bubbles that implode upon contact with contaminants, dislodging dirt, grease, oils, and other particles from the surface of the object being cleaned.
Ultrasonic cleaning is favored for its precision and efficiency, as it can clean delicate or intricate components without causing physical damage. The process is also highly effective for cleaning hard-to-reach areas and small parts that cannot be easily cleaned using traditional methods.
Ultrasonic cleaning instruments can be broadly classified based on their design, scale, and intended use. Each type serves specific functions, from small personal devices to large industrial cleaning systems.
2. Types of Ultrasonic Cleaning Instruments Based on Size and Scale
Ultrasonic cleaning instruments come in various sizes, each designed for a specific level of use. The classification based on size includes small-scale, medium-scale, and large-scale ultrasonic cleaners. Each size comes with its own set of features and applications.
2.1. Small-Scale Ultrasonic Cleaners
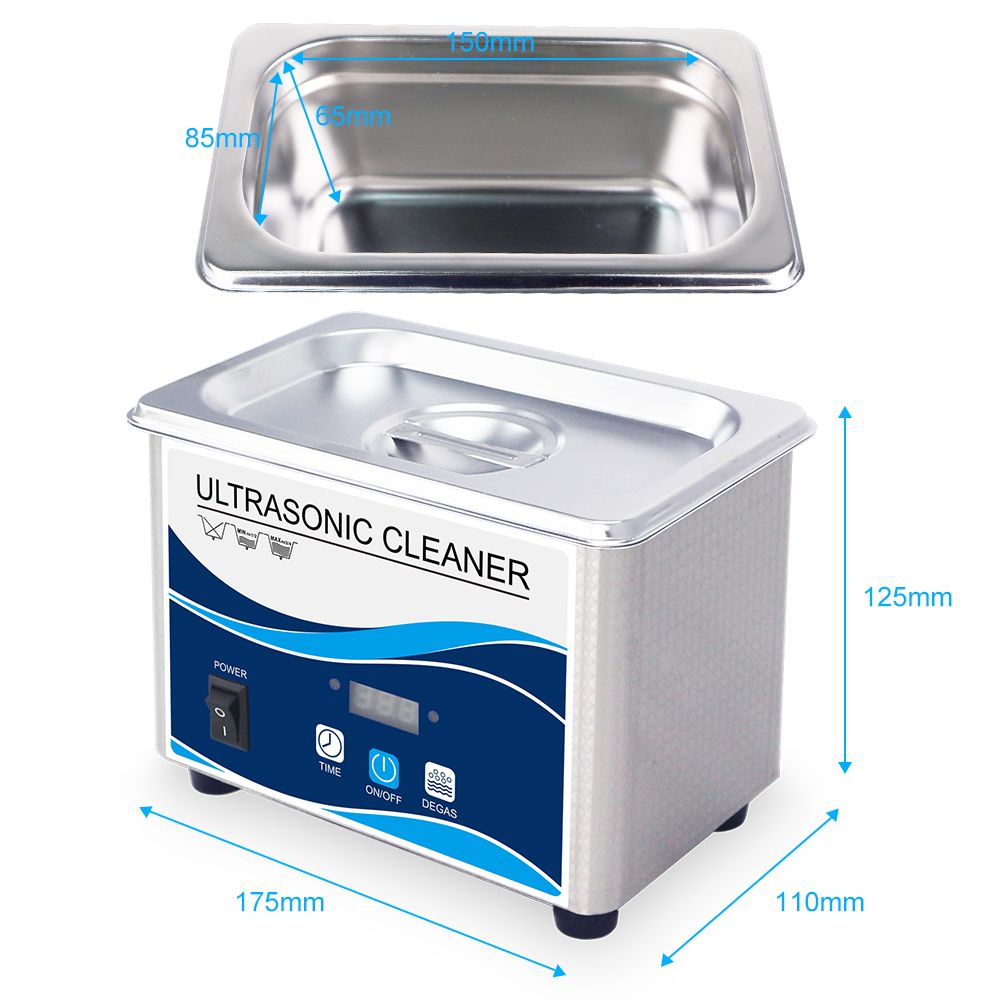
Small-scale ultrasonic cleaning instruments are compact, portable devices typically used for cleaning jewelry, dental instruments, electronic components, or laboratory equipment. These devices are perfect for personal use or small business operations that require high-precision cleaning without the need for large industrial machines.
Features:
- Compact design, often table-top or benchtop models.
- Lower cleaning capacity, ideal for smaller parts.
- Generally cost-effective and easy to use.
- Commonly used in homes, small workshops, or dental clinics.
Small-scale ultrasonic cleaners usually operate with a frequency range between 30 kHz and 40 kHz. This frequency is ideal for cleaning delicate items such as watches, eyeglasses, and dental tools, where precision is critical.
2.2. Medium-Scale Ultrasonic Cleaners
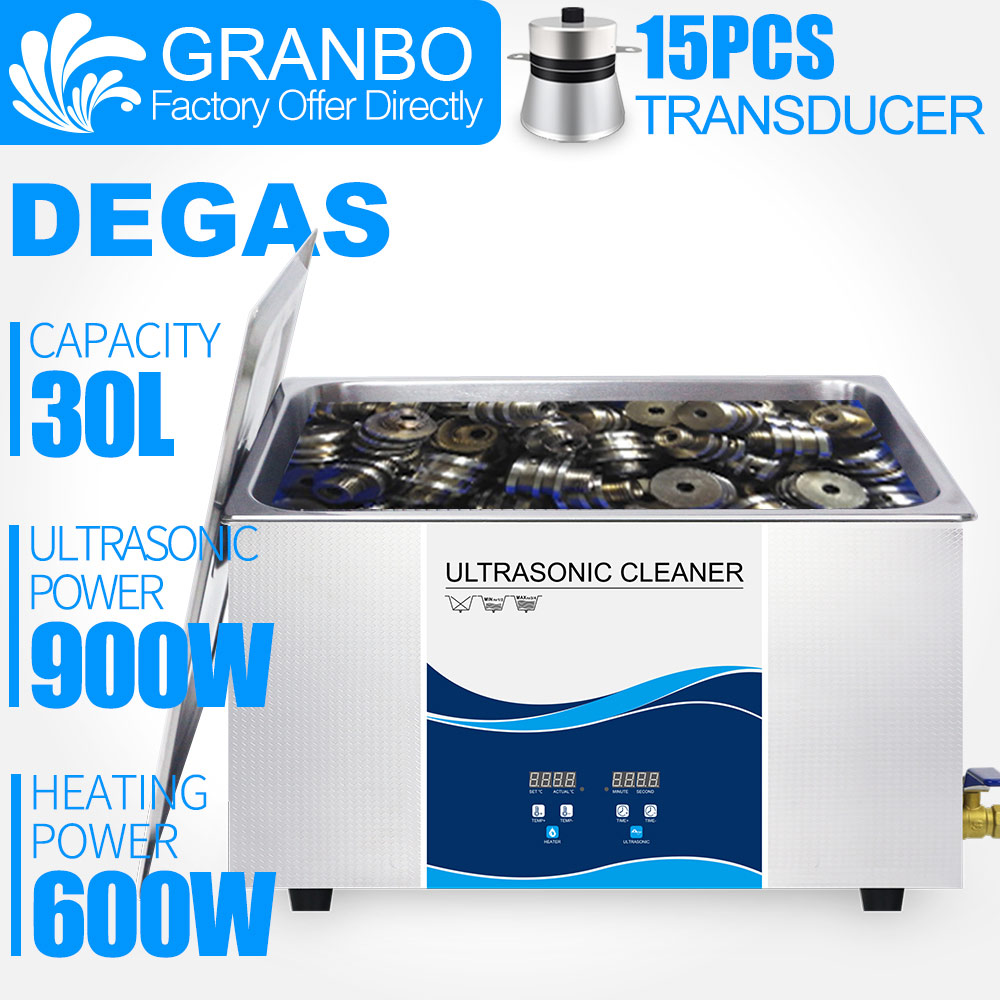
Medium-scale ultrasonic cleaning systems are more powerful and can handle larger quantities of parts. These instruments are typically found in laboratories, small manufacturing units, or maintenance facilities that require higher throughput. They are more robust than small-scale cleaners but still manageable for less intensive cleaning applications.
Features:
- Larger tanks and higher cleaning capacity than small-scale devices.
- Suitable for cleaning larger components such as automotive parts, medical instruments, and machine tools.
- Often feature customizable cleaning cycles for varying applications.
Medium-scale cleaners typically operate in the range of 25 kHz to 50 kHz frequencies. The wider frequency range allows for more flexibility in cleaning different types of contaminants and materials, making them suitable for more industrial applications.
2.3. Large-Scale Ultrasonic Cleaners
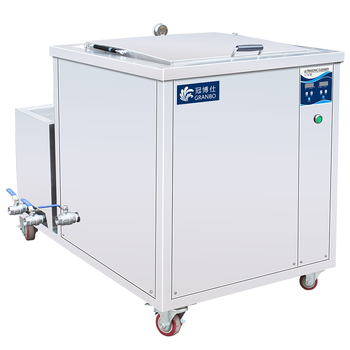
Large-scale ultrasonic cleaning systems are designed for heavy-duty industrial cleaning, capable of handling larger objects or bulk quantities of parts. These cleaners are used in industries such as automotive manufacturing, aerospace, and medical device production, where high throughput and large-scale cleaning operations are essential.
Features:
- High power output for more aggressive cleaning.
- Large tanks and multiple transducers for extensive cleaning capacity.
- Can clean parts with complex geometries or multiple components simultaneously.
- Often equipped with automated features for seamless integration into production lines.
Large-scale ultrasonic cleaners operate at lower frequencies (typically between 20 kHz and 40 kHz), which provides the cavitation energy needed to clean heavily soiled or large industrial parts.
3. Classifications Based on Application
Ultrasonic cleaning systems are also classified based on their specific application, ensuring that the technology is adapted to the varying needs of different industries. The main categories include:
3.1. Jewelry and Precision Parts Cleaners
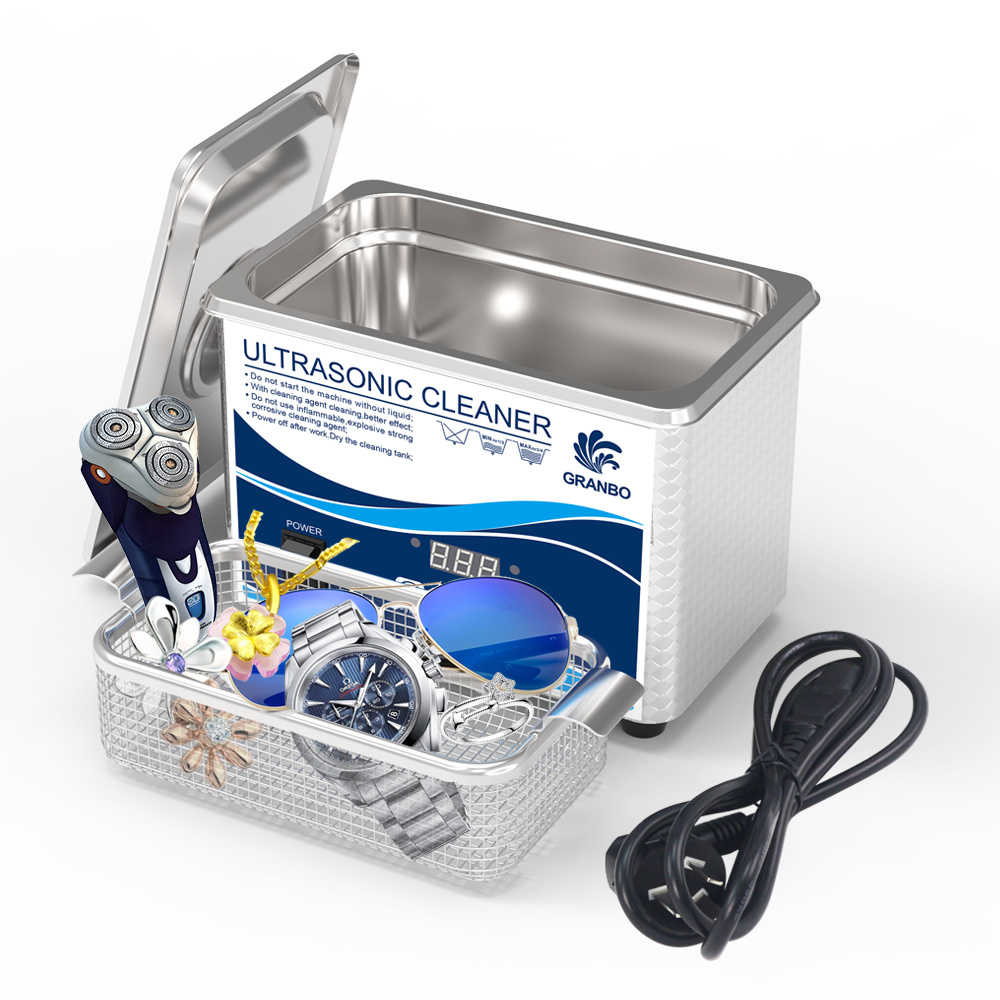
These ultrasonic cleaners are specifially designed for cleaning delicate items such as jewelry, watches, and small electronic components. The main challenge in cleaning such items is the risk of damage, so these systems often feature high-frequency settings and adjustable power to ensure a gentle yet thorough cleaning process.
Features:
- Higher frequencies (around 40 kHz to 70 kHz) to ensure precision.
- Soft cleaning solutions or water-based detergents to prevent damage.
- Often include baskets or specialized holders to prevent scratching during the cleaning process.
Jewelry cleaners, for instance, require ultrasonic systems with precision settings to remove dirt and oils from the intricate details of gemstones and metals without scratching or damaging the surface.
3.2. Medical and Laboratory Ultrasonic Cleaners
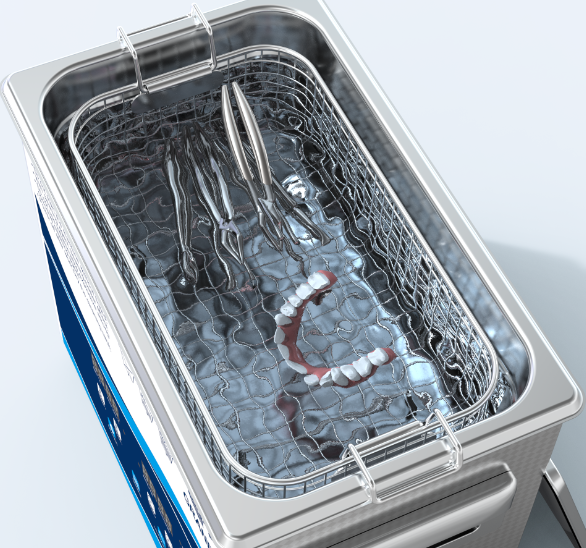
Medical ultrasonic cleaners are designed for sterilizing and cleaning surgical instruments, dental tools, and other medical equipment. They need to meet strict hygiene and safety standards, which is why many of these systems are equipped with advanced features such as filtration and temperature control. Laboratory ultrasonic cleaners are similarly used for cleaning test tubes, petri dishes, and other sensitive lab equipment.
Features:
- High precision to ensure thorough sterilization without damaging equipment.
- Often equipped with digital controls to manage time, temperature, and cleaning cycles.
- Specialized cleaning solutions for biological contaminants or stubborn stains.
The ultrasonic cleaning process in medical applications often involves a sterilization cycle that ensures all surfaces are free from contaminants, making it crucial for patient safety and infection control.
3.3. Industrial Ultrasonic Cleaners
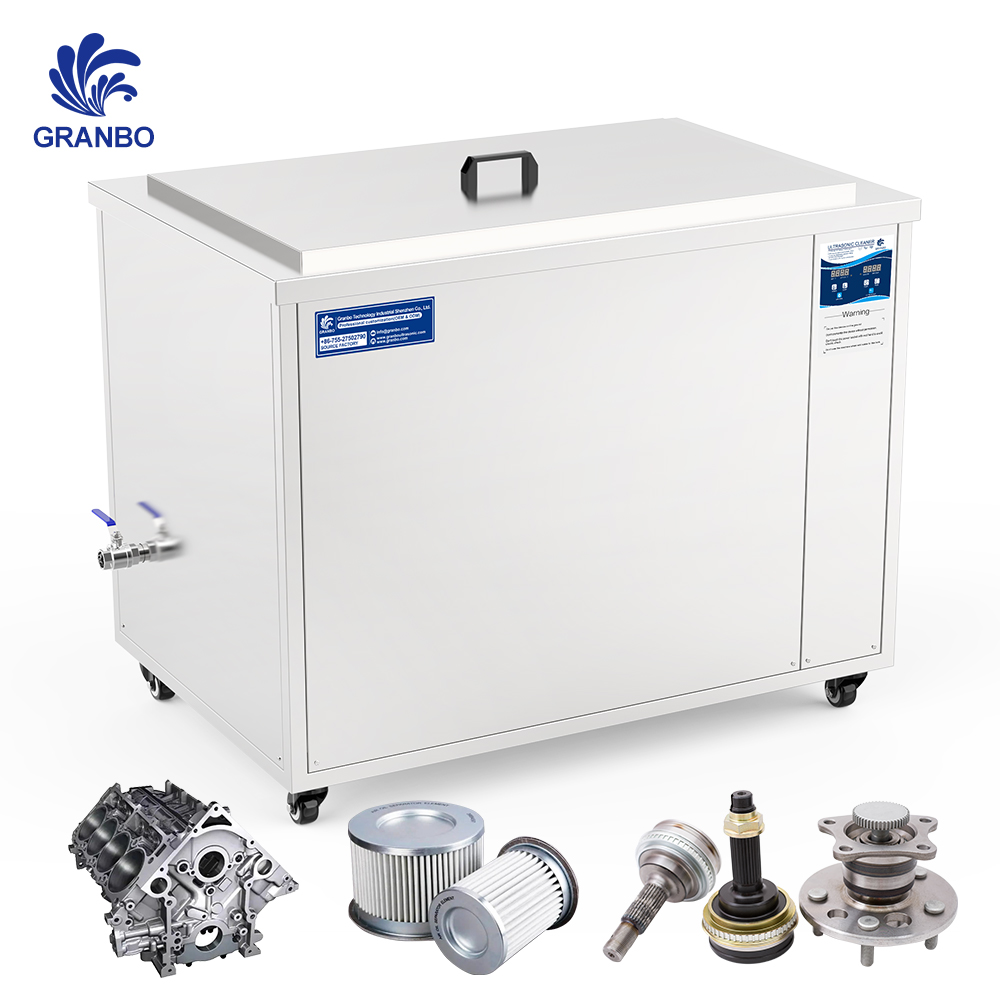
Industrial ultrasonic cleaners are used for cleaning heavy-duty components in manufacturing and maintenance industries. These systems are typically larger, more powerful, and capable of cleaning complex parts with heavy dirt, oils, and other residues. Industrial ultrasonic cleaners are essential in industries such as aerospace, automotive, and electronics, where maintaining cleanliness and precision is critical to product quality.
Features:
- High power for cleaning large and heavily contaminated parts.
- Multi-frequency capabilities for versatility.
- Robust construction for handling demanding environments and high-volume cleaning.
These cleaners are often automated and designed to integrate with production lines, reducing manual labor and enhancing operational efficiency.
4. Classifications Based on Cleaning Methodology
Ultrasonic cleaning systems can also be classified by their cleaning methodologies. This classification includes traditional ultrasonic cleaning, dual-frequency ultrasonic cleaning, and ultrasonic cleaning combined with other cleaning technologies.
4.1. Traditional Ultrasonic Cleaning
This is the most common method of ultrasonic cleaning, which uses a single frequency (typically between 20 kHz and 40 kHz) for all cleaning tasks. The cleaning process involves immersing the item in a cleaning solution, and the ultrasonic waves create cavitation bubbles that help dislodge contaminants from the surface.
4.2. Dual-Frequency Ultrasonic Cleaning
Dual-frequency ultrasonic cleaners are equipped with two frequencies, allowing users to switch between them depending on the cleaning task. The advantage of dual-frequency systems is that they offer flexibility, providing better cleaning power for larger or heavily soiled parts at lower frequencies, and finer cleaning at higher frequencies for delicate items.
4.3. Hybrid Cleaning Systems.
Hybrid systems combine ultrasonic cleaning with other cleaning technologies, such as laser cleaning, plasma cleaning, or chemical cleaning. These systems are ideal for industries that require specific cleaning performance for challenging contaminants or applications.
5. Future Trends in Ultrasonic Cleaning Instruments
The ultrasonic cleaning industry is constantly evolving, driven by innovations in technology, materials, and application requirements. Several key trends are shaping the future of ultrasonic cleaning instruments:
5.1. Automation and Integration with Industry 4.0
Automation is one of the most important trends in ultrasonic cleaning. As industries move toward Industry 4.0 principles, there is an increasing demand for fully automated ultrasonic cleaning systems that can integrate into smart factories. These systems can offer real-time monitoring, remote control, and data analysis, ensuring optimal performance and reduced downtime.
5.2. Enhanced Efficiency and Sustainability
With growing concerns about environmental impact, there is a significant push toward making ultrasonic cleaning systems more energy-efficient and sustainable. This includes the development of cleaner, biodegradable detergents, more efficient transducers, and systems that use less water and power while maintaining cleaning performance.
5.3. Miniaturization and Personal Devices
As ultrasonic cleaning technology becomes more accessible, miniaturization is also a key trend. Smaller ultrasonic cleaning devices designed for personal use, such as ultrasonic jewelry cleaners or personal electronics cleaners, are becoming increasingly popular among consumers.
Conclusion
The diversity of ultrasonic cleaning instruments reflects the technology’s wide-ranging capabilities. From small personal devices to large industrial machines, ultrasonic cleaners are becoming indispensable across many sectors. As technology continues to evolve, we can expect even more efficient, precise, and sustainable solutions to emerge, further enhancing the versatility of ultrasonic cleaning in industries worldwide.
References:
- Zhang, W., & Wang, Q. (2020). “Advancements in Ultrasonic Cleaning Technology: Design and Applications.” Journal of Industrial Cleaning, 38(5), 145-160.
- Liu, Y., & Zhao, J. (2021). “Ultrasonic Cleaning: Theory and Applications in Medical Devices and Industrial Manufacturing.” International Journal of Precision Engineering, 34(2), 42-55.
- Johnson, P., & Miller, D. (2019). “The Future of Ultrasonic Cleaning in Industry: Trends and Innovations.” Industrial Technology Review, 48(11), 123-137.