Optical lens ultrasonic cleaning machine is a member of the big family of ultrasonic cleaning machines. Each tank is 38 L. The main purpose is to clean glass lenses, resin lenses, microscopes, telescopes, camera lenses, coated glass, prisms, lenses and other optical products before and after coating. And to clean between processes before assembly to meet the product manufacturing process and quality requirements.
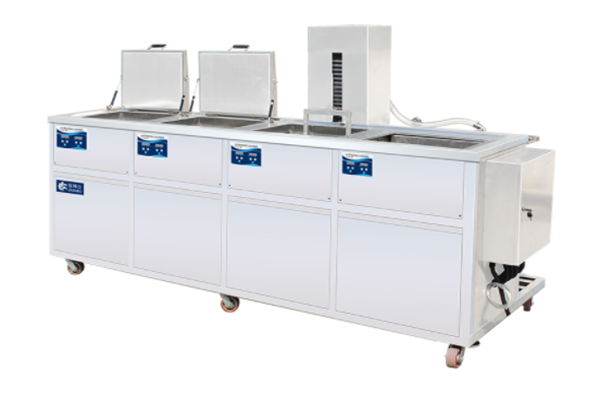
Granbo specializes in manufacturing ultrasonic cleaning machines for optical lenses. There are many successful cases. The process is generally cleaning, rinsing, filtering and drying to remove dust, watermarks, fingerprints and impurities from the lens surface.
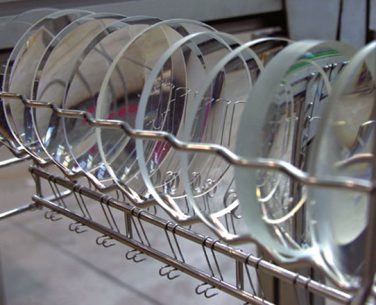
Optical lens ultrasonic cleaning machine cleaning principle.
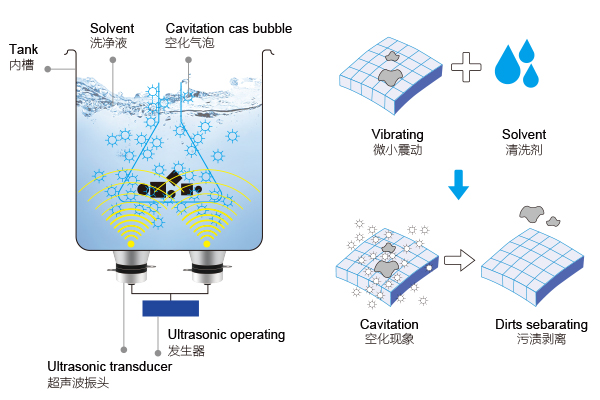
Ultrasonic cleaning is the use of ultrasonic cavitation, acceleration and direct current in the liquid directly or indirectly acting on the liquid and dirt, so that the dirt layer is dispersed, emulsified and stripped, thus achieving the purpose of cleaning. In the current use of ultrasonic cleaning machine, the use of more cavitation and direct into the flow.
1, the unique slow pull dehydration, circulating hot air drying method instead of the traditional solvent dehydration, safe and environmentally friendly;
2, with filtering circulation system;
3, multi-slot ultrasonic cleaning process, to ensure the cleaning effect.
Why use optical lens ultrasonic cleaning machine?
Optical glass is mixed with high purity silicon, boron, sodium, potassium, zinc, lead, magnesium, calcium, barium and other oxides according to a specific formula, melted at high temperature in a platinum crucible, stirred evenly with ultrasonic waves to remove air bubbles; then cooled slowly for a long time to avoid internal stress in the glass block. After cooling, the glass block must be measured by optical instruments to test the purity, transparency, uniformity, refractive index and dispersion are in line with specifications. The qualified glass blocks are heated and forged into optical lens blanks. In the optical industry, the cleanliness of the lens is required to be relatively high. The main cleaning of lenses after polishing residual polishing solution, adhesives, protective materials cleaning; lenses after grinding edge grinding oil, glass powder cleaning; lenses before coating fingerprints, drool ring and a variety of adhesion cleaning. The traditional cleaning method is to use wiping materials (gauze, dust-free paper) with chemical reagents (gasoline, ethanol, acetone, ether) for manual cleaning by means of soaking and wiping. This method is time-consuming and laborious, poor cleaning degree, obviously not adapted to the modern scale of optical cold processing industry. This forces people to find a mechanized cleaning means to replace. So the ultrasonic cleaning machine technology gradually optical cold processing industry and show their skills, and further promote the development of the optical cold processing industry.
Ultrasonic cleaning can probably be understood as ultrasonic waves to more than 20,000 times per second compression force and decompression interactivity of high-frequency transformations to the liquid for transmission. In the decompression effect, the liquid produces the phenomenon of vacuum nucleus group bubble, and in the compressive force effect, the vacuum nucleus group bubble is crushed by the pressure to produce a strong impact, thus stripping the dirt on the surface of the object to be cleaned, so as to achieve the purpose of precision cleaning. Since the optical industry has extremely strict requirements for lens cleanliness, the choice of cleaning agent is very important. While considering the cleaning ability of a certain cleaning agent, it is also important to consider its corrosiveness and other aspects.