Bearing manufacturing is a rapidly developing supporting industry in modern industry. All rotary motion equipment or devices, bearings are indispensable key components, and its performance and quality directly affects the performance and service life of the equipment. In terms of improving product quality, how to improve the cleanliness of bearings is a very important part.
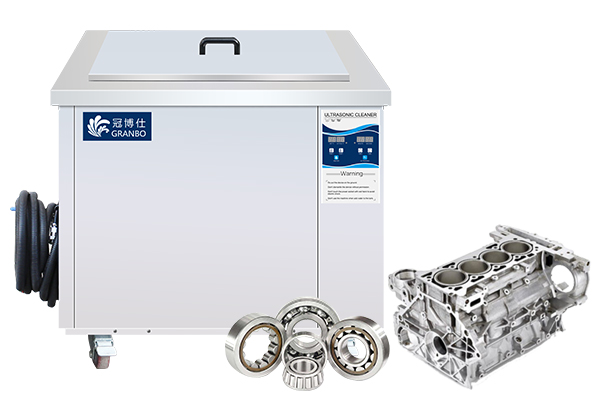
Bearing cleaning characteristics
Bearing parts in the mechanical processing, heat treatment and assembly process, its surface are adhered with many inorganic and organic pollutants. The main pollutants of bearings are processing lubricants, heat treatment oil, chips, dust, etc. The focus of cleaning is grease pollutants, grease cleaning off, other pollutants will also lose the ability to adhere.
Bearing parts are generally made of ferrous alloys, which produce varying degrees of magnetism during processing. The chip page particles adsorbed by ferromagnetism should also be removed in the demagnetization process.
Bearing cleaning must be dry to prevent rusting, and the cleaning end process should have anti-rust measures.
Demagnetizer principle and structure
In the spray cleaning and ultrasonic cleaning process, the bearing if there is still magnetic, the adsorption of metal chips on the bearing will be difficult to be cleaned off. Therefore, the bearings must be demagnetized before spray cleaning, and the main function of demagnetizer is to demagnetize the bearings.
Demagnetizer is composed of demagnetizer shell (containing iron core and excitation coil) and demagnetizer controller. According to the structure of the demagnetizer is divided into three types of material channel type, gantry type and flat type, the specific specifications of the shape size can be designed according to the size of the workpiece.
Two important conditions for demagnetization are: 1) overlapping of magnetic poles; 2) decreasing magnetic field strength.
Among them, there are three ways of magnetic poles overlapping: 1, the magnetization current adopts AC; 2, alternately changing the direction of DC; 3, changing the direction of the specimen in the magnetic field.
And there are two ways of decreasing magnetic field strength: 1, the test piece gradually away from the magnetic field or magnetic field gradually away from the test piece; 2, the power supply control current decay or segmentation step down.
Bearing cleaning fluid selection
In view of the main dirt bearing cleaning is the characteristics of grease, generally do not recommend the use of water-based cleaning. Water-based cleaning equipment consumes a lot of water, attached to the water treatment equipment and bearing cleaning equipment covers an area of large, high energy consumption, long process route, relatively low efficiency.
According to the law of similar solubility of cleaning, solvent-based cleaning fluids have a great advantage in dissolving grease, and waste liquid separation and recycling equipment is simple, high efficiency, is widely used. The optional cleaning fluids are transitional alternative solvents HCFCs class, containing stabilizers and hydrocarbon propane class solvent cleaning fluid.
Bearing ultrasonic cleaning process introduction
① Process one: [demagnetization] → [solvent soaking + ultrasonic washing] → [solvent rinsing] → [vapor phase rinsing ten dry]
a.The ultrasonic frequency is 28~40kHz selectable, and the power can be adjusted according to the size of the workpiece.
b. Soaking, sonication and rinsing are all in the same solvent.
c. General room temperature soaking and washing, such as the use of n-bromopropane can be heated to 50 ℃, vapor phase washing temperature that is n-bromopropane boiling point temperature 71 ℃.
d. When the bearings are no longer condensed in the steam layer, the workpiece drying is completed, and can be raised after a short stay in the condensation area.
②Process two: [demagnetization] → [solvent spray wash 1] → [solvent ultrasonic cleaning + inner ring rotation] → [solvent spray wash 2 + inner ring rotation] → [air knife blowing and cutting 1] → [air knife blowing and cutting 2 ten inner ring rotation] → [hot air drying]
a.Ultrasonic frequency is 28~40kHz selectable, power can be adjusted according to the size of the workpiece.
b. Soaking, ultrasonic, spraying are the same solvent.
c. Select hydrocarbon cleaning solution, the distillation range in 140 ~ ~ 190 ℃ volatile small, the equipment sealing requirements are not high.
d. It can be completely volatilized at room temperature or heated condition, but the compressed air must be filtered when drying with hot air, the accuracy of the hot air filter used is 0.1pm, and the hot air temperature is adjusted to 60~65℃, there is no residue after drying with hot air.
e. Non-toxic, safer for the cleaning operator. There will be no corrosion and rust on the bearing material.
f. Bearing cleaning positioning (rotation in inner ring cleaning).