In the fast-paced world of electronics manufacturing, maintaining the integrity and functionality of components is paramount. One of the most effective methods for ensuring the cleanliness and reliability of electronic parts is the ultrasonic cleaning process. This advanced technique leverages high-frequency sound waves to remove contaminants from even the most intricate and delicate components, offering a level of precision that traditional cleaning methods simply cannot match.
The Science Behind Ultrasonic Cleaning
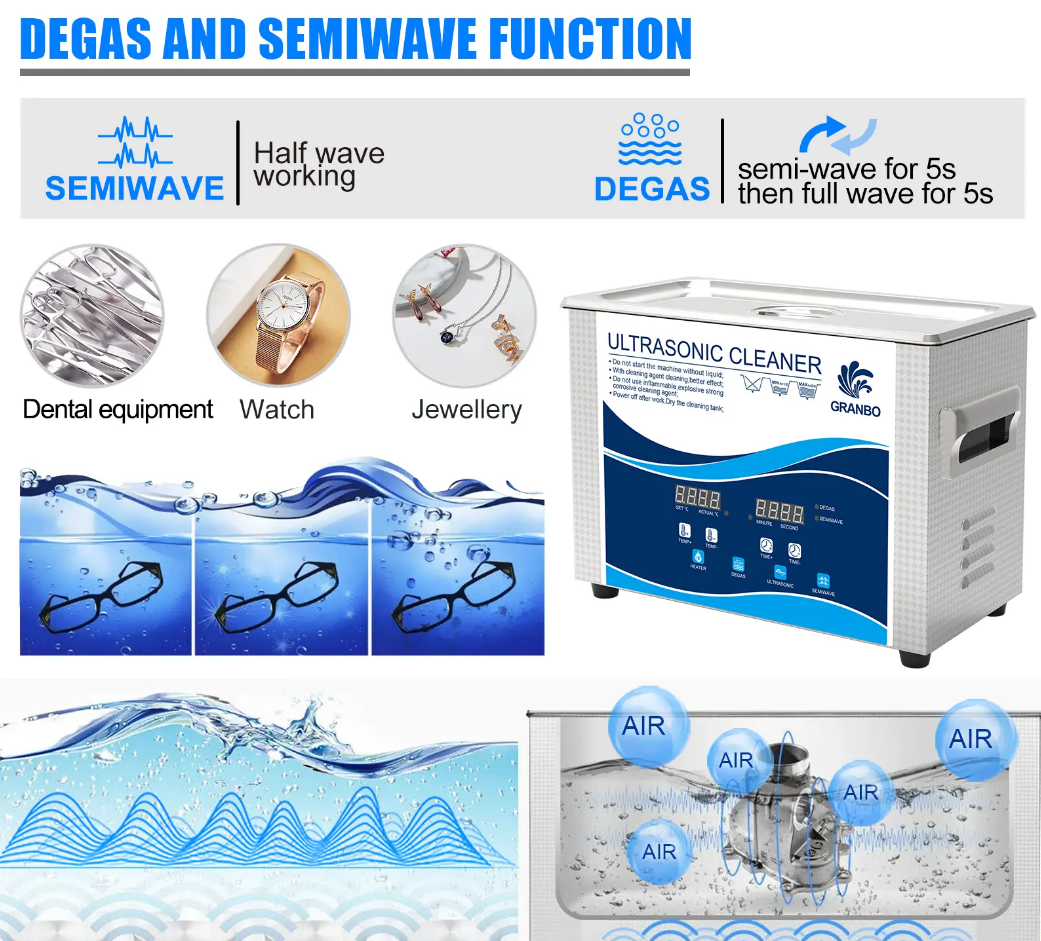
Ultrasonic cleaning is based on the principle of cavitation, a process where high-frequency sound waves create microscopic bubbles in a liquid medium. These bubbles implode upon contact with surfaces, generating intense localized energy that dislodges dirt, grease, and other contaminants. The frequency of the sound waves typically ranges from 20 kHz to 40 kHz, with higher frequencies used for more delicate components to prevent damage.
The cleaning solution, often a mixture of water and specialized detergents, plays a crucial role in the process. It enhances the cavitation effect and ensures that contaminants are effectively dissolved and removed. The choice of solution depends on the type of contaminants and the material of the components being cleaned.
The image above illustrates the cavitation process, highlighting the microscopic bubbles that form and collapse to clean electronic components.
Why Ultrasonic Cleaning is Ideal for Electronic Components
Electronic components, such as circuit boards, connectors, and sensors, are often characterized by complex geometries and tight tolerances. Traditional cleaning methods, such as manual scrubbing or solvent immersion, can be ineffective or even damaging. Ultrasonic cleaning, on the other hand, offers several advantages:
1. Precision Cleaning: The cavitation effect reaches into the smallest crevices and holes, ensuring thorough cleaning without the need for disassembly.
2. Non-Destructive: Unlike abrasive methods, ultrasonic cleaning does not cause wear or damage to delicate parts.
3. Efficiency: The process is fast and can clean multiple components simultaneously, reducing downtime and increasing productivity.
4. Environmental Benefits: By minimizing the use of harsh chemicals and reducing waste, ultrasonic cleaning is a more sustainable option.
The Ultrasonic Cleaning Process: Step by Step
The ultrasonic cleaning process for electronic components typically involves the following steps:
1. Preparation: Components are inspected and pre-cleaned to remove large debris. This step ensures that the ultrasonic cleaner can focus on finer contaminants.
2. Immersion: The components are placed in a cleaning tank filled with the appropriate solution. The tank is equipped with ultrasonic transducers that generate the sound waves.
3. Cleaning: The ultrasonic cleaner is activated, and the cavitation process begins. The duration of this step depends on the level of contamination and the type of components.
4. Rinsing: After cleaning, the components are rinsed with deionized water to remove any residual cleaning solution.
5. Drying: The components are dried using air knives, ovens, or other drying methods to prevent water spots or corrosion.
Applications of Ultrasonic Cleaning in the Electronics Industry
Ultrasonic cleaning is widely used across various sectors of the electronics industry, including:
1. Printed Circuit Board (PCB) Manufacturing: PCBs are prone to contamination from flux residues, solder paste, and dust. Ultrasonic cleaning ensures that these contaminants are removed without damaging the board’s delicate traces.
2. Semiconductor Production: In the production of semiconductors, even microscopic contaminants can affect performance. Ultrasonic cleaning provides the precision needed to maintain high yields.
3. Medical Electronics: Devices such as pacemakers and imaging equipment require absolute cleanliness to ensure patient safety. Ultrasonic cleaning meets the stringent standards of the medical industry.
4. Aerospace and Defense: Electronic components used in these industries must withstand extreme conditions. Ultrasonic cleaning ensures that they are free from contaminants that could compromise their performance.
Innovations and Future Trends in Ultrasonic Cleaning
As technology advances, so too does the field of ultrasonic cleaning. Some of the most exciting developments include:
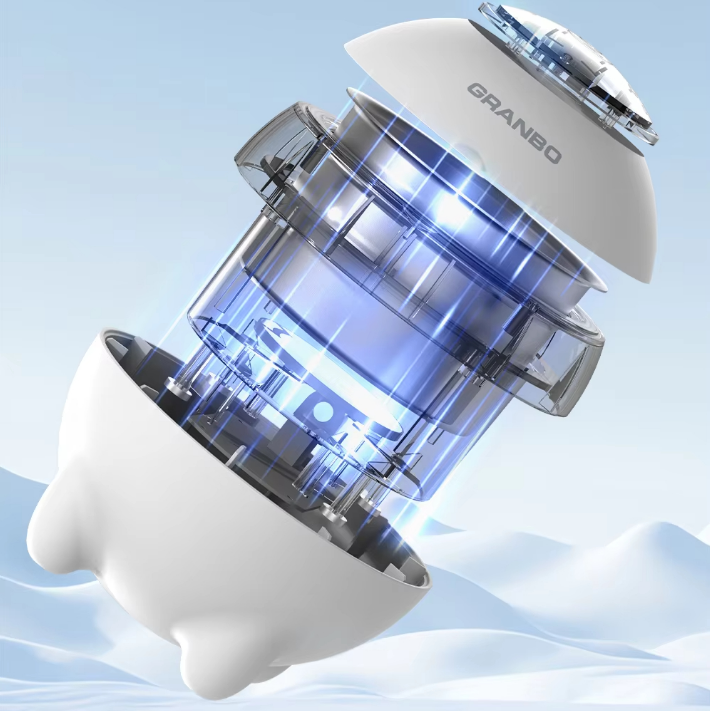
1. Flexible Cleaning Solutions: New systems are being designed to accommodate a wider range of component sizes and shapes, making the process even more versatile.
2. Integration with Automation: Automated loading and unloading systems, combined with advanced robotics, are streamlining the cleaning process and reducing labor costs.
3. Eco-Friendly Solutions: Researchers are developing biodegradable cleaning agents and energy-efficient ultrasonic systems to further reduce the environmental impact.
4. AI and Machine Learning: These technologies are being used to optimize cleaning parameters, such as frequency and duration, for specific components and contaminants.
The ultrasonic cleaning process has become an indispensable tool in the electronics industry, offering unmatched precision, efficiency, and sustainability. As innovations continue to emerge, this technology will play an increasingly important role in ensuring the reliability and performance of electronic components. By embracing these advancements, manufacturers can stay ahead of the curve and deliver products that meet the highest standards of quality and safety.
References
1. Curie, J., & Curie, P. (1880). “Développement, par pression, de l’électricité polaire dans les cristaux hémièdres à faces inclinées.” Comptes Rendus de l’Académie des Sciences, 91, 294-295.
2. Jaffe, B., Cook, W. R., & Jaffe, H. (1971). Piezoelectric Ceramics*. Academic Press.
3. Smith, W. A., & Auld, B. A. (1991). “Modeling 1-3 composite piezoelectrics: Thickness-mode oscillations.” IEEE Transactions on Ultrasonics, Ferroelectrics, and Frequency Control, 38(1), 40-47.
4. Uchino, K. (2000). Ferroelectric Devices. CRC Press.
5. Zhang, Q. M., & Li, J. F. (2012). “Piezoelectric materials for high power, high temperature applications.” Materials Today, 15(11), 478-486.
6. “Application of Ultrasonic Cleaning Machine in Electromagnesium Industry.” Tullker News, 2024.
7. “Ultrasonic cleaning system – ROBOSONIC – Keer International.” DirectIndustry, 2022.
8. “Ultrasonic Industrial Cleaning – by Jumpy Man Industrial Cleaning.” Jumpy Man’s Industrial Cleaning, 2025.