Ultrasonic cleaning equipment has become an indispensable tool across various industries, from healthcare to manufacturing, due to its ability to deliver precise and efficient cleaning results. The technology leverages high-frequency sound waves to create cavitation bubbles in a liquid medium, which implode upon contact with surfaces, effectively removing contaminants. However, not all ultrasonic cleaning systems are created equal. The design of these devices plays a critical role in their performance, efficiency, and suitability for specific applications. This article delves into the basic design types of ultrasonic cleaning equipment, providing a detailed overview of their features, advantages, and use cases.
1. Benchtop Ultrasonic Cleaners: Compact and Versatile.
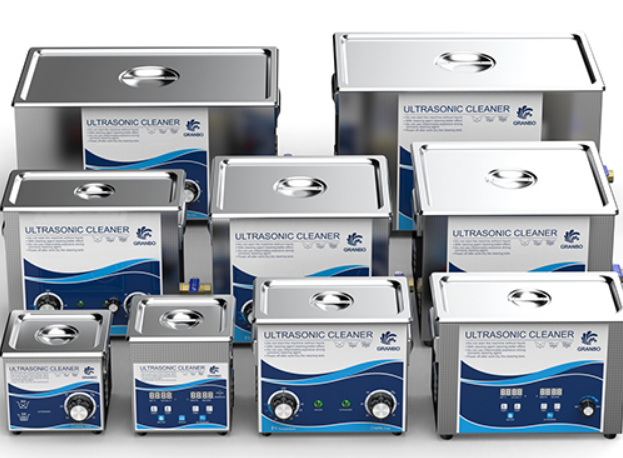
Benchtop ultrasonic cleaners are among the most common and widely used designs. As the name suggests, these units are small enough to fit on a laboratory bench or workstation, making them ideal for environments where space is limited. They are typically used for cleaning small to medium-sized items, such as jewelry, dental instruments, and electronic components.
These cleaners are characterized by their portability, ease of use, and affordability. Most benchtop models feature a stainless steel tank, a digital control panel for adjusting parameters like frequency and temperature, and a transducer system that generates ultrasonic waves. They are available in a range of tank sizes, from a few liters to larger capacities, catering to diverse cleaning needs.
One of the key advantages of benchtop ultrasonic cleaners is their versatility. They can be used with a variety of cleaning solutions, including water-based detergents, solvents, and specialized chemicals, depending on the application. However, their compact size also limits the volume of items that can be cleaned at once, making them less suitable for industrial-scale operations.
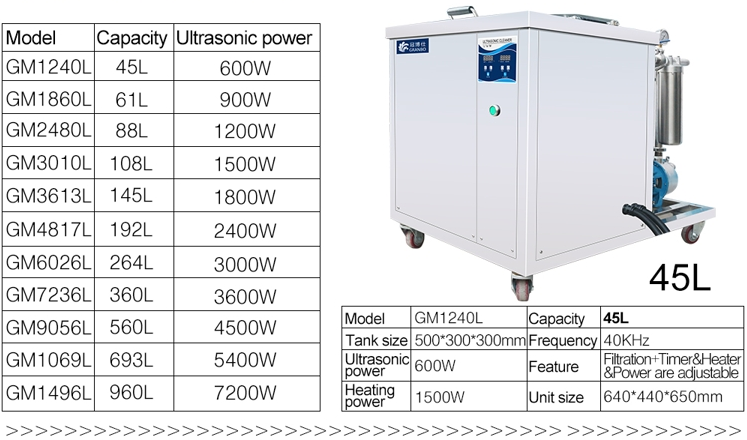
2. Industrial Ultrasonic Cleaners: Power and Precision for Heavy-Duty Applications
Industrial ultrasonic cleaners are designed to handle large-scale cleaning tasks, making them a staple in manufacturing, automotive, and aerospace industries. These systems are built to accommodate heavy and bulky items, such as engine parts, machinery components, and large tools. Unlike benchtop models, industrial cleaners are often custom-designed to meet specific operational requirements.
The defining features of industrial ultrasonic cleaners include their robust construction, high-capacity tanks, and powerful transducers capable of generating intense ultrasonic waves. Many industrial models also incorporate advanced features like automated loading and unloading systems, multi-stage cleaning cycles, and integrated drying mechanisms. These enhancements not only improve efficiency but also ensure consistent cleaning results.
Another notable aspect of industrial ultrasonic cleaners is their scalability. They can be configured as standalone units or integrated into larger production lines, allowing for seamless automation. While these systems are more expensive than their benchtop counterparts, their ability to handle complex cleaning tasks and reduce labor costs makes them a worthwhile investment for large-scale operations.
3. Immersion Ultrasonic Cleaners: Targeted Cleaning for Delicate Items
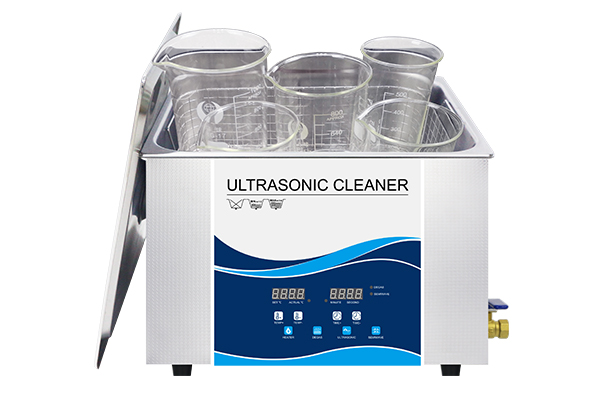
Immersion ultrasonic cleaners are specialized devices designed for cleaning delicate or intricate items that require precise and gentle treatment. These systems feature a small tank or chamber filled with a cleaning solution, into which the items are submerged. The ultrasonic waves are then directed at the submerged objects, ensuring thorough cleaning without causing damage.
This design is particularly popular in industries like healthcare, where delicate instruments such as surgical tools and endoscopes need to be cleaned meticulously. Immersion cleaners are also used in the electronics industry for cleaning circuit boards and other sensitive components. The ability to control parameters like frequency and power output allows users to tailor the cleaning process to the specific requirements of the items being cleaned.
One of the standout features of immersion ultrasonic cleaners is their ability to clean hard-to-reach areas, such as crevices and internal channels, which are often inaccessible with traditional cleaning methods. However, their limited capacity and specialized design make them less suitable for general-purpose cleaning tasks.
4. Multi-Tank Ultrasonic Cleaners: Efficiency Through Sequential Processing
Multi-tank ultrasonic cleaners are designed for applications that require multiple cleaning stages, such as washing, rinsing, and drying. These systems consist of several interconnected tanks, each dedicated to a specific stage of the cleaning process. Items are transferred from one tank to another, either manually or via an automated conveyor system, ensuring a thorough and efficient cleaning cycle.
This design is particularly beneficial in industries where contamination control is critical, such as pharmaceuticals and food processing. By separating the cleaning, rinsing, and drying stages, multi-tank systems minimize the risk of cross-contamination and ensure that items are cleaned to the highest standards. Additionally, the use of multiple tanks allows for the simultaneous processing of large volumes of items, significantly improving productivity.
While multi-tank ultrasonic cleaners offer numerous advantages, they are also more complex and expensive than single-tank models. Their installation and maintenance require careful planning and expertise, making them more suitable for large-scale operations with specialized cleaning needs.
5. Custom Ultrasonic Cleaning Systems: Tailored Solutions for Unique Challenges
In some cases, off-the-shelf ultrasonic cleaning equipment may not meet the specific requirements of a particular application. This is where custom ultrasonic cleaning systems come into play. These systems are designed and built to address unique challenges, such as cleaning unusually shaped items, handling hazardous materials, or integrating with existing production lines.
Custom ultrasonic cleaners can be tailored in terms of size, shape, power output, and functionality. For example, a custom system might include specialized transducers for enhanced cavitation, a unique tank configuration to accommodate oversized items, or advanced filtration systems for handling contaminated cleaning solutions. The design process typically involves close collaboration between the manufacturer and the end-user to ensure that the final product meets all operational and regulatory requirements.
While custom systems offer unparalleled flexibility and performance, they also come with higher costs and longer lead times. However, for industries with highly specialized cleaning needs, the investment in a custom solution can yield significant long-term benefits.
The Role of Frequency and Power in Ultrasonic Cleaning Design
Beyond the physical design of the equipment, the choice of ultrasonic frequency and power output plays a crucial role in determining the effectiveness of the cleaning process. Low-frequency ultrasonic waves (20-40 kHz) are ideal for removing heavy contaminants and cleaning large, robust items, while high-frequency waves (80 kHz and above) are better suited for delicate items and fine cleaning tasks. Some advanced systems offer variable frequency settings, allowing users to switch between different frequencies based on the application.
Power output, measured in watts per gallon, is another critical factor. Higher power levels generate more intense cavitation, resulting in faster and more thorough cleaning. However, excessive power can damage delicate items or cause erosion of the cleaning tank. Therefore, it is essential to strike a balance between power and frequency to achieve optimal cleaning results.
Choosing the Right Ultrasonic Cleaning Equipment for Your Needs
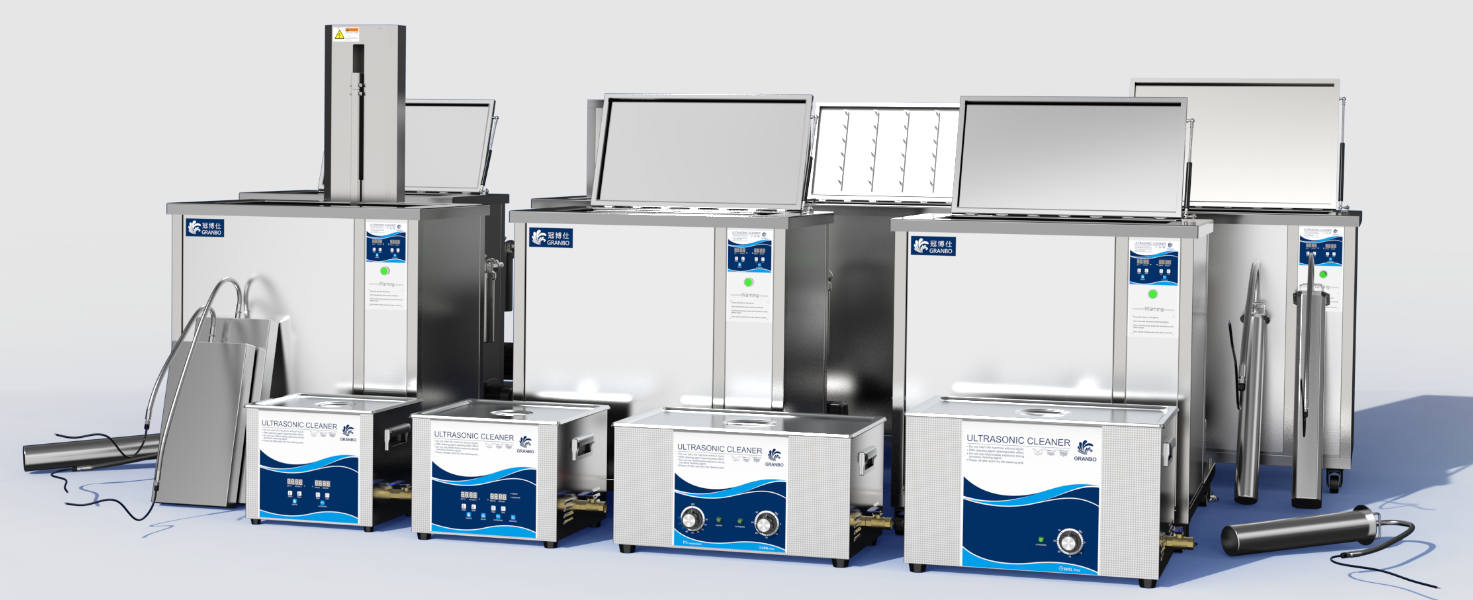
Selecting the appropriate ultrasonic cleaning equipment requires careful consideration of several factors, including the type and volume of items to be cleaned, the nature of the contaminants, and the specific requirements of the application. Benchtop models are ideal for small-scale operations and delicate items, while industrial systems are better suited for heavy-duty tasks and large volumes. Immersion and multi-tank cleaners offer specialized solutions for unique challenges, and custom systems provide the ultimate flexibility for highly specific needs.
By understanding the different design types and their respective advantages, businesses can make informed decisions that enhance their cleaning processes, improve efficiency, and reduce operational costs. Whether you are cleaning jewelry in a small workshop or maintaining complex machinery in a large manufacturing facility, there is an ultrasonic cleaning solution designed to meet your needs.
References
1. Mason, T. J., & Lorimer, J. P. (2002). Applied Sonochemistry: Uses of Power Ultrasound in Chemistry and Processing. Wiley-VCH.
2. Gallego-Juárez, J. A., & Graff, K. F. (2015). Power Ultrasonics: Applications of High-Intensity Ultrasound. Woodhead Publishing.
3. Ensminger, D., & Bond, L. J. (2011). Ultrasonics: Fundamentals, Technologies, and Applications. CRC Press.
4. Povey, M. J. W. (1997). Ultrasonic Techniques for Fluids Characterization. Academic Press.
5. FDA Guidelines for Cleaning Medical Devices. U.S. Food and Drug Administration. Retrieved from [www.fda.gov](https://www.fda.gov).