The Fundamentals of Ultrasonic Cleaning Equipment
Ultrasonic cleaning technology is widely recognized for its ability to remove contaminants from intricate surfaces using high-frequency sound waves. The efficiency of ultrasonic cleaning depends significantly on the design of the equipment, which varies based on industry requirements, object size, and the nature of contaminants. By understanding the different types of ultrasonic cleaning systems, businesses can select the most appropriate design for their specific needs.
Ultrasonic cleaning systems generate sound waves in a liquid medium, producing microscopic cavitation bubbles that implode upon contact with surfaces. This process effectively removes grease, dirt, biofilms, and other residues without damaging delicate components. The effectiveness of ultrasonic cleaning largely depends on the frequency, power output, and type of transducers used in the equipment.
Single-Tank Ultrasonic Cleaning Systems
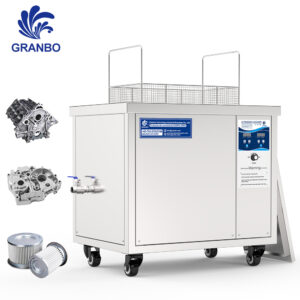
One of the most common types of ultrasonic cleaning equipment is the single-tank system. As the name suggests, this design consists of a single chamber where items are placed for cleaning. These systems are ideal for small-scale applications and are commonly used in industries such as jewelry cleaning, dental instrument sterilization, and small automotive parts maintenance.
Key Features:
- Compact and cost-effective design.
- Suitable for light to moderate contamination removal.
- Often includes heating elements to enhance cleaning efficiency.
- Available in different frequency ranges to accommodate various materials.
While single-tank systems offer convenience and efficiency, they may not be suitable for large-scale industrial applications due to limited capacity and lack of multi-stage cleaning options.
Multi-Tank Ultrasonic Cleaning Systems
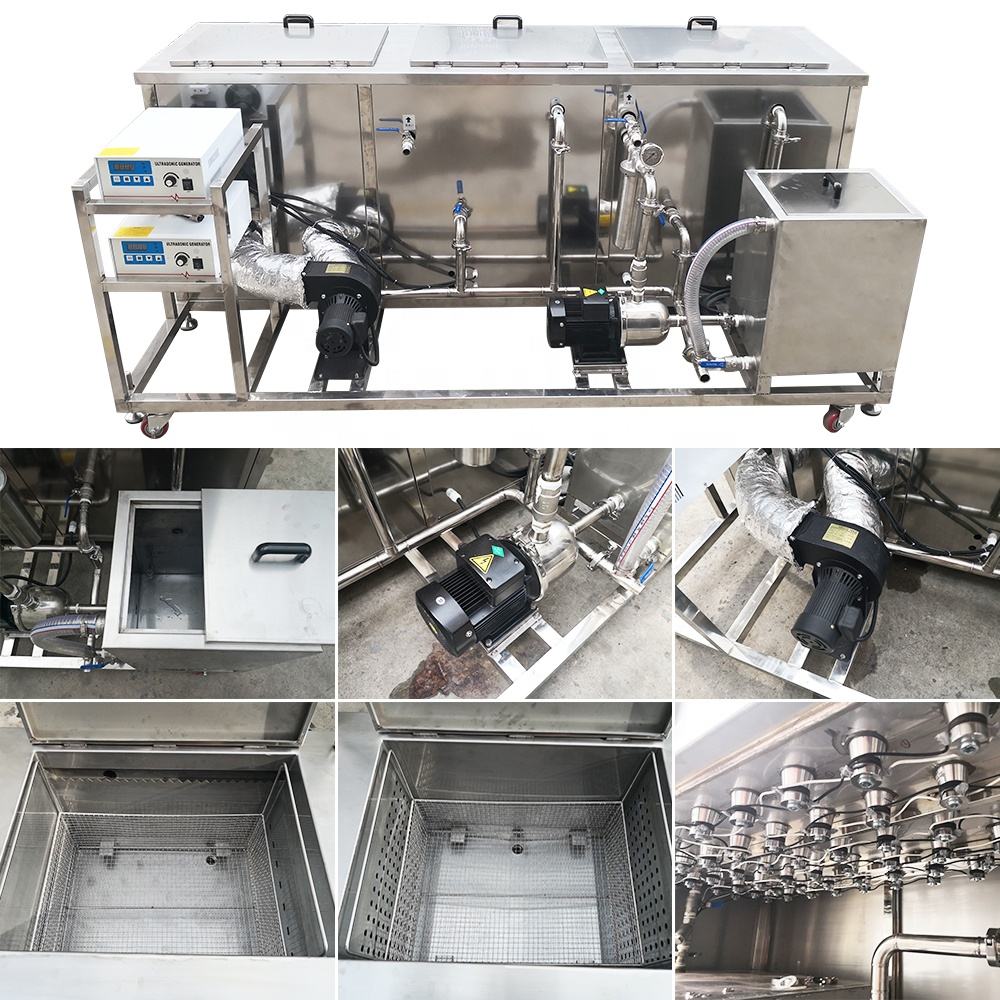
For more complex cleaning needs, multi-tank ultrasonic cleaning systems provide a more advanced solution. These setups incorporate multiple stages, allowing for pre-cleaning, ultrasonic cleaning, rinsing, and drying in a single workflow. Industries such as aerospace, medical device manufacturing, and precision engineering rely on these systems for thorough decontamination.
Key Features:
- Multiple tanks for sequential cleaning processes.
- Ideal for industries requiring high levels of cleanliness.
- Can include automated conveyor systems for efficiency.
- Supports different cleaning solutions for varied contamination types.
Multi-tank systems provide an enhanced level of cleanliness but require a higher initial investment and more space for installation.
Benchtop Ultrasonic Cleaners
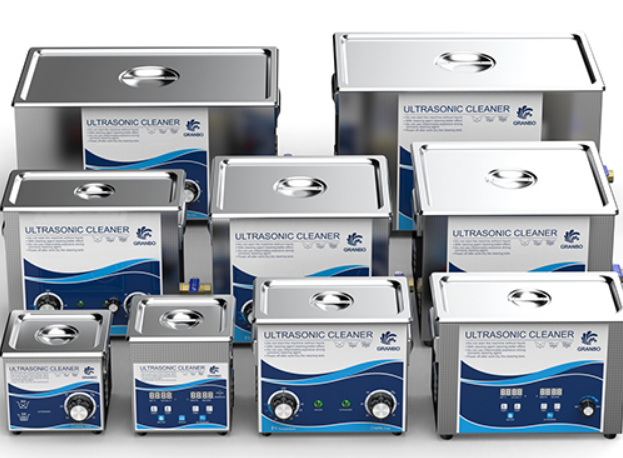
Benchtop ultrasonic cleaners are compact models designed for use in laboratories, dental clinics, and electronics repair shops. These units offer a balance between affordability and performance, making them suitable for applications that demand precision cleaning on a small scale.
Key Features:
- Portable and space-saving design.
- Suitable for delicate instruments and small parts.
- User-friendly controls for quick operation.
- Available with digital timers and temperature control settings.
Despite their convenience, benchtop cleaners are not intended for heavy-duty industrial cleaning and have limited capacity compared to larger systems.
Industrial-Scale Ultrasonic Cleaning Systems
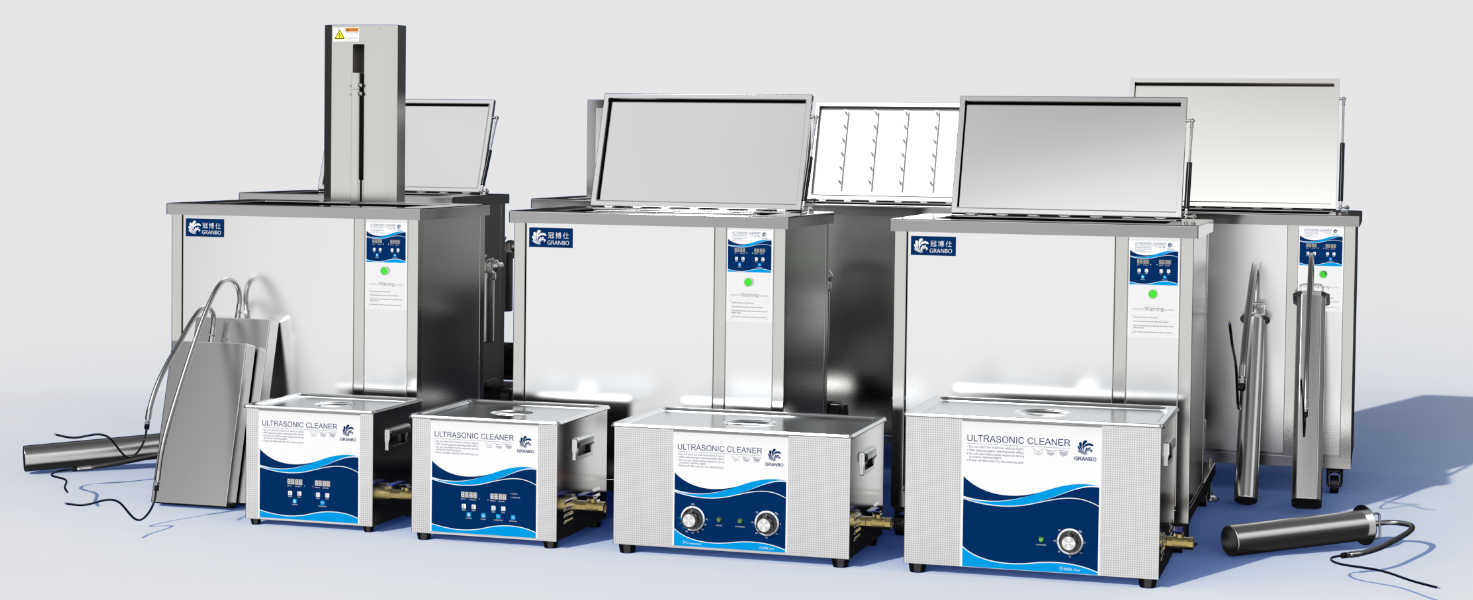
Large-scale ultrasonic cleaning systems are designed for heavy-duty applications such as automotive manufacturing, aviation, and metal fabrication. These systems feature robust construction and advanced automation to handle high volumes of components efficiently.
Key Features:
- Large tank capacity to accommodate bulky items.
- High-powered transducers for enhanced cavitation effects.
- Programmable controls for precision cleaning cycles.
- May integrate with robotic handling systems for automation.
These systems offer unparalleled cleaning efficiency but require substantial space, investment, and maintenance.
Factors to Consider When Choosing an Ultrasonic Cleaning System
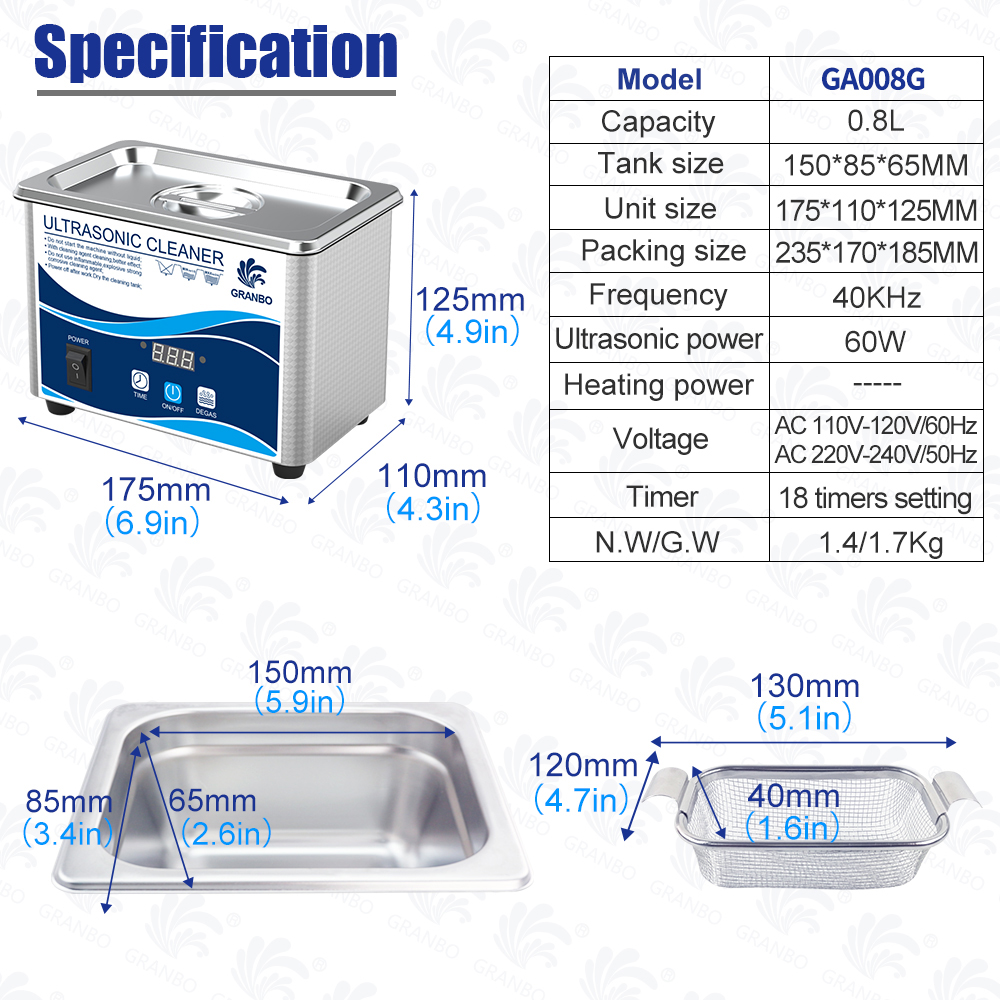
Selecting the right ultrasonic cleaner involves evaluating several factors, including:
- Frequency Requirements: Lower frequencies (20-40 kHz) are best for heavy-duty cleaning, while higher frequencies (80-130 kHz) are ideal for delicate surfaces.
- Tank Capacity: Ensuring the tank size fits the objects to be cleaned.
- Automation Needs: Some industries benefit from robotic-assisted cleaning to improve efficiency.
- Solution Compatibility: Different contaminants require specific cleaning solutions for optimal results.
- Regulatory Compliance: Industries such as healthcare and food processing must adhere to strict cleaning standards.
As ultrasonic cleaning technology continues to evolve, newer models integrate smart sensors, AI-powered diagnostics, and eco-friendly cleaning solutions to enhance efficiency and sustainability. Understanding these design variations helps businesses and professionals make informed decisions when investing in ultrasonic cleaning equipment.
References
- Suslick, K. S. (1990). “Sonochemistry.” Science, 247(4949), 1439-1445. doi:10.1126/science.247.4949.1439
- Mason, T. J. (2000). “Advances in Sonochemistry: Ultrasonic Cleaning.” Ultrasonics Sonochemistry, 7(4), 147-149. doi:10.1016/S1350-4177(99)00028-2
- Nyborg, W. L. (1982). “Ultrasound: Its Chemical, Physical, and Biological Effects.” Journal of the Acoustical Society of America, 71(6), 1629-1635. doi:10.1121/1.387911