The Fundamentals of Ultrasonic Cleaning Machines
Ultrasonic cleaning machines have become indispensable in various industries, from medical and electronics to automotive and aerospace. These machines utilize high-frequency sound waves to generate cavitation bubbles in a cleaning solution, effectively removing contaminants from intricate surfaces. Their ability to clean without causing physical damage makes them superior to conventional cleaning methods. Understanding their structural components and core design principles is essential for optimizing performance and ensuring longevity.
Structural Composition of an Ultrasonic Cleaning Machine
The overall design of an ultrasonic cleaning machine comprises several key structural components that work together to deliver efficient cleaning. These components include the transducer system, generator, cleaning tank, control panel, and filtration system. Each part plays a crucial role in ensuring that the machine operates at peak efficiency.
- Cleaning Tank – The heart of the ultrasonic cleaner, the cleaning tank is typically made of stainless steel to withstand prolonged exposure to cleaning solutions and cavitation energy.
- Ultrasonic Transducers – These devices convert electrical energy into mechanical vibrations, producing the sound waves responsible for cavitation.
- Ultrasonic Generator – The electronic unit that powers the transducers, controlling frequency and power output to achieve optimal cleaning results.
- Control Panel – Modern ultrasonic cleaners feature digital or analog control panels that regulate temperature, frequency, and cleaning time.
- Filtration and Circulation System – Some machines incorporate a filtration system to maintain cleaning solution purity, especially in industrial applications.
Core Components and Their Functions
Each ultrasonic cleaning machine depends on well-designed core components to function effectively. The following key components influence performance and durability:
1. Ultrasonic Transducers: The Driving Force Behind Cleaning
The ultrasonic transducer is the most critical component in an ultrasonic cleaning machine. It converts electrical signals into mechanical vibrations, creating the cavitation effect that cleans surfaces. There are three main types of transducers:
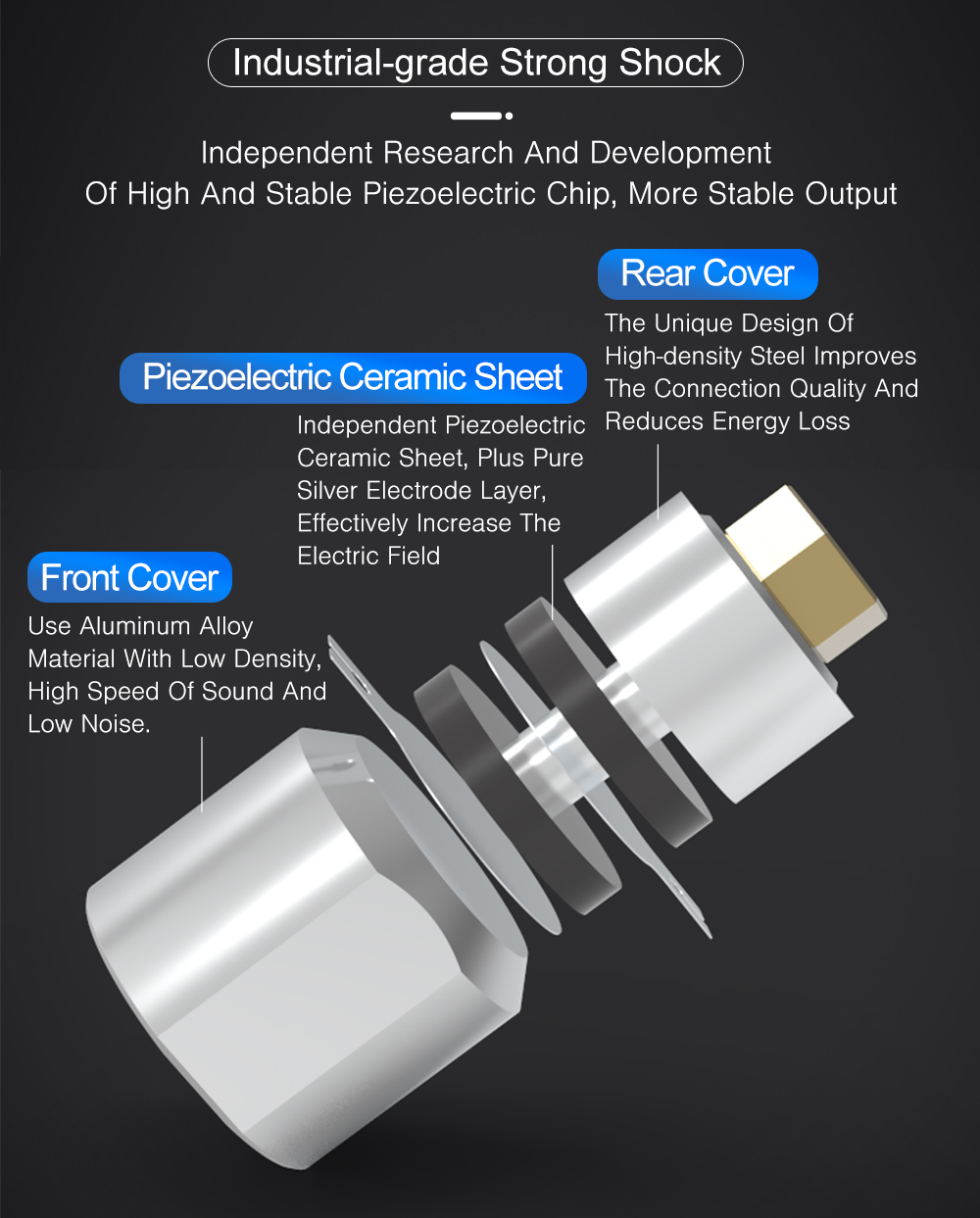
- Magnetostrictive Transducers – Known for durability and high power output, commonly used in industrial applications.
- Piezoelectric Transducers – More commonly found in commercial ultrasonic cleaners due to their efficiency and affordability.
- Hybrid Transducers – Combining both technologies to achieve optimal performance and energy efficiency.
The placement of transducers within the cleaning tank also affects cleaning uniformity, with bottom-mounted and side-mounted configurations offering different advantages.
2. Ultrasonic Generator: Regulating Frequency and Power
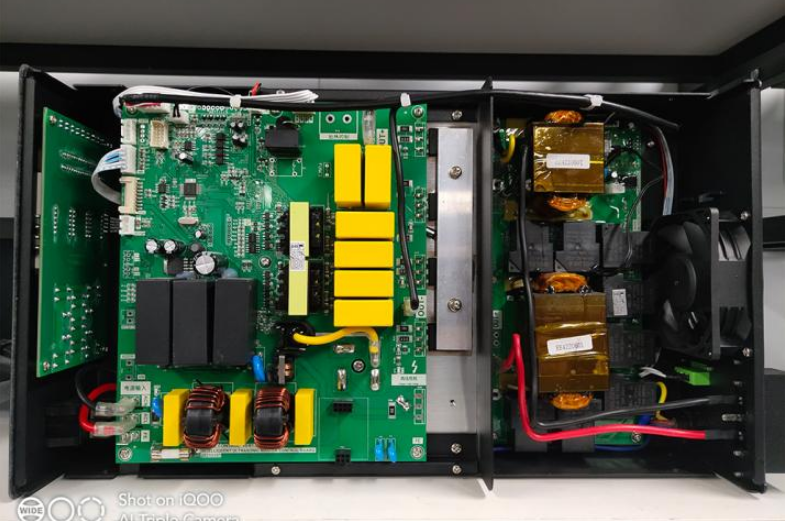
The ultrasonic generator acts as the control hub, dictating the performance of the cleaning machine. Key factors influencing generator efficiency include:
- Frequency Control – Most ultrasonic cleaning machines operate between 20 kHz and 80 kHz, with lower frequencies generating larger cavitation bubbles for heavy-duty cleaning and higher frequencies used for delicate applications.
- Power Output – A higher wattage ensures more powerful cavitation but must be carefully balanced to avoid surface damage.
- Pulse and Sweep Technology – Advanced generators incorporate these features to enhance cleaning effectiveness and uniformity.
3. Cleaning Tank: Material and Design Considerations
The cleaning tank must be robust enough to handle continuous cavitation activity. Important factors influencing tank performance include:
- Material – Stainless steel (typically SUS304 or SUS316) ensures resistance to corrosion and prolonged durability.
- Thickness – The thickness of the tank walls directly impacts energy efficiency and longevity.
- Resonance Optimization – Proper design ensures that sound waves distribute evenly, minimizing dead zones.
4. Control System: Enhancing User Experience
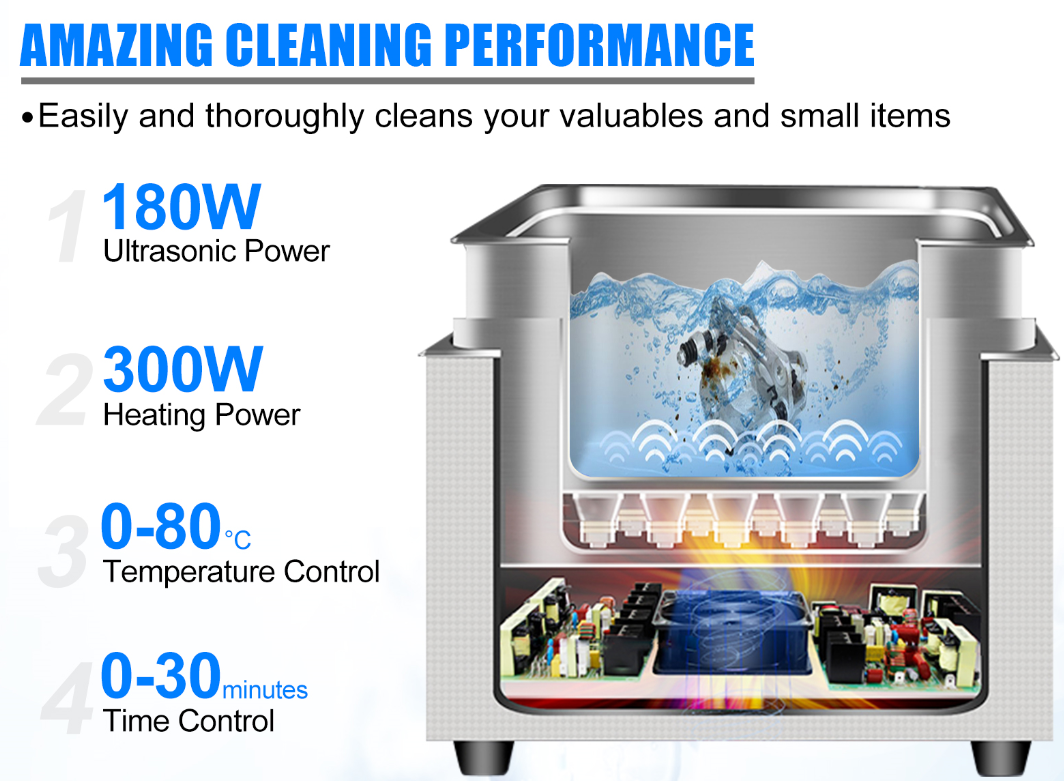
A well-integrated control system allows operators to fine-tune cleaning parameters. Digital control panels often include:
- Temperature Regulation – Heating the cleaning solution improves detergent efficacy.
- Timer Functions – Allowing precise control over cleaning cycles.
- Variable Frequency Settings – Providing flexibility for different cleaning applications.
Future Trends in Ultrasonic Cleaning Technology
The field of ultrasonic cleaning technology is continuously evolving, with innovations aimed at improving efficiency and expanding applications. Emerging trends include:
- Smart Ultrasonic Cleaners – Integrating IoT-enabled monitoring for real-time diagnostics and remote operation.
- Eco-Friendly Cleaning Solutions – Reducing reliance on chemical solvents and utilizing biodegradable detergents.
- Multi-Frequency Systems – Providing greater flexibility in cleaning applications by allowing adjustable frequencies within a single unit.
- Microscopic and Nano-Cleaning Applications – Advancing the technology to cater to ultra-precision industries such as semiconductor fabrication and biomedical research.
Ultrasonic cleaning machines continue to be an essential tool across multiple industries, driven by advancements in component design and system optimization. By refining the structure, enhancing transducer efficiency, and integrating intelligent control systems, these machines will remain at the forefront of precision cleaning technologies.
References
- Mason, T. J., & Peters, D. (2002). Practical Sonochemistry: Uses and Applications of Ultrasound. Ellis Horwood Limited.
- Ensminger, D., & Bond, L. J. (2011). Ultrasonics: Fundamentals, Technologies, and Applications. CRC Press.
- Awad, T. S., Moharram, H. A., Shaltout, O. E., Asker, D., & Youssef, M. M. (2012). Applications of ultrasound in analysis, processing, and quality control of food: A review. Food Research International, 48(2), 410-427.
- Leighton, T. G. (1994). The Acoustic Bubble. Academic Press.
- Krefting, D., & Giese, U. (2019). Development of efficient ultrasonic cleaning systems for industrial applications. Journal of Ultrasonic Technology, 35(3), 215-228.