Ultrasonic generators are an essential component in a range of industrial and commercial processes. These devices convert electrical energy into ultrasonic energy, which is then used for various applications such as cleaning, medical treatments, material testing, and even food processing. The rise of ultrasonic technology has transformed industries by enabling precise and efficient operations. Whether it’s a small handheld unit or a large industrial machine, ultrasonic generators play a crucial role in ensuring these processes are carried out effectively. In this article, we explore the workings of ultrasonic generators, their applications across various sectors, and the benefits they offer.
1. What Is an Ultrasonic Generator?
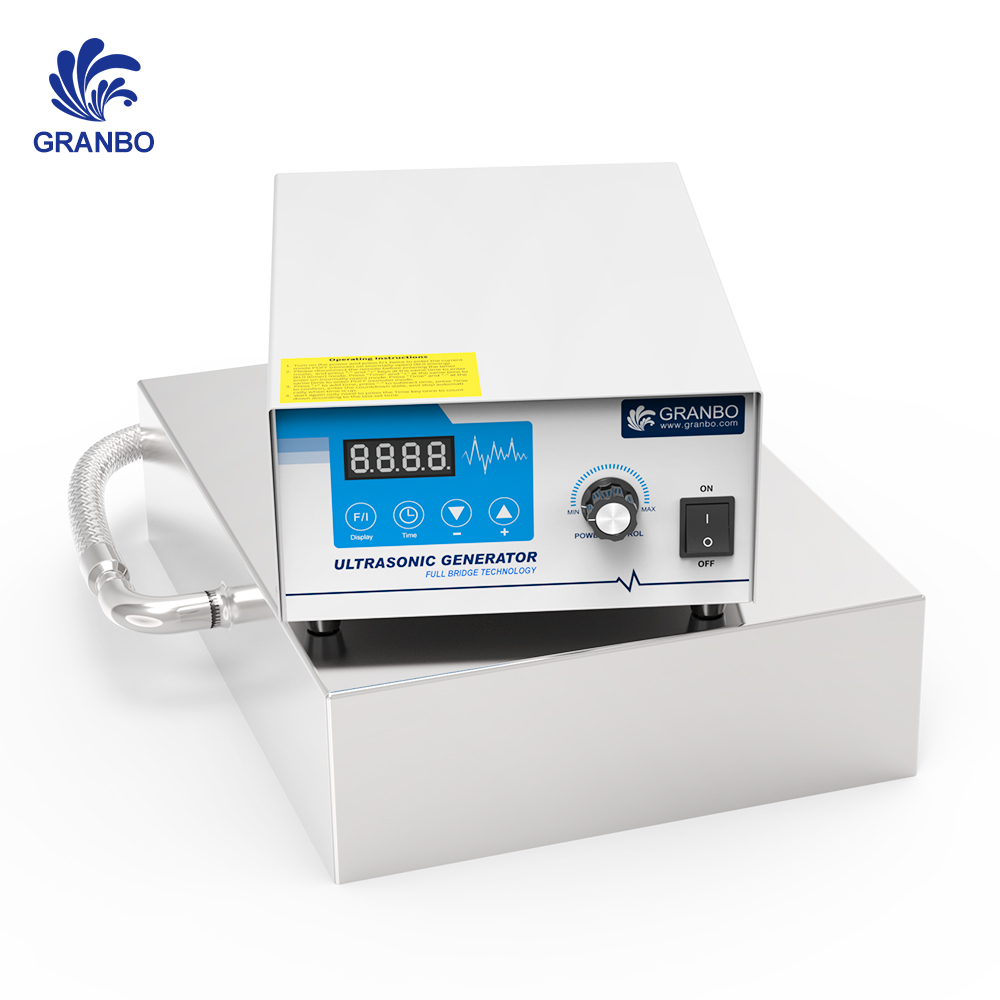
An ultrasonic generator is a device that produces high-frequency sound waves, typically in the range of 20 kHz to several MHz, which are then transmitted into a medium such as water, air, or other liquids. The generator powers a transducer, which converts electrical energy into mechanical energy, producing the ultrasonic waves. These waves propagate through the medium, creating tiny pressure variations and high-frequency vibrations that are capable of breaking down substances, cleaning surfaces, or inducing chemical reactions.
The core function of the ultrasonic generator is to supply a consistent electrical signal that drives the transducer, allowing for the production of these ultrasonic waves. The generator is designed to maintain the frequency and amplitude of the waves to ensure they remain stable and effective throughout the process.
2. Components of an Ultrasonic Generator
An ultrasonic generator consists of several key components, each playing a vital role in the generation and transmission of ultrasonic waves:
- Power Supply: Provides the necessary electrical energy to the system.
- Oscillator Circuit: Converts the power supply’s energy into an alternating current (AC) signal.
- Amplifier: Boosts the signal from the oscillator to a level that can drive the transducer.
- Matching Network: Ensures the correct impedance matching between the generator and the transducer, maximizing the efficiency of energy transfer.
- Transducer: The part of the ultrasonic system that converts the electrical signal into mechanical vibrations (ultrasonic waves).
- Control Panel: Allows the user to adjust parameters such as frequency, amplitude, and power output.
Each of these components must be carefully designed and calibrated to ensure optimal performance in specific applications, whether for cleaning, welding, or medical treatments.
3. How Do Ultrasonic Generators Work?
Ultrasonic generators function by generating high-frequency electrical signals. These signals are fed into a transducer, which typically consists of piezoelectric crystals that can change their shape when an electrical current passes through them. The transducer then converts these electrical signals into mechanical vibrations, creating sound waves at ultrasonic frequencies.
These sound waves create cavitation bubbles when they travel through a liquid. The bubbles implode, generating intense localized energy that can be used for cleaning, mixing, or dislodging particles. In some cases, the ultrasonic waves also generate heat, which further enhances the effectiveness of the process, especially in cleaning and disinfection applications.
The frequency and amplitude of the ultrasonic waves can be adjusted based on the specific needs of the application. For instance, higher frequencies are often used for cleaning delicate items, while lower frequencies may be better suited for more aggressive cleaning tasks.
4. Applications of Ultrasonic Generators
Ultrasonic generators find use in numerous industries and applications, demonstrating their versatility. Here are some of the key areas where they are widely utilized:
4.1. Cleaning Applications
One of the most common uses of ultrasonic generators is in cleaning processes. Ultrasonic cleaning uses high-frequency sound waves to agitate a cleaning solution, creating microscopic bubbles that remove dirt, grease, oils, and other contaminants from surfaces. This technique is particularly effective for cleaning delicate items, such as jewelry, medical instruments, electronic components, and automotive parts.
In industries like healthcare and manufacturing, ultrasonic cleaning is invaluable for maintaining equipment hygiene and ensuring precise cleaning without causing any damage to sensitive parts.
4.2. Medical and Dental Uses
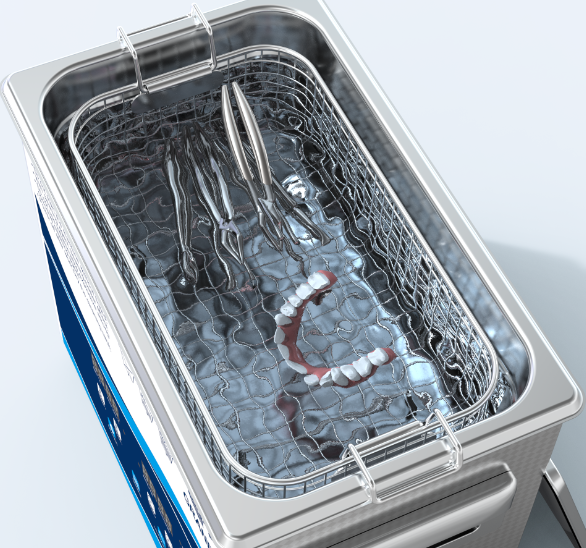
In the medical field, ultrasonic generators are utilized for a range of purposes, including diagnostic imaging and therapeutic treatments. For example, ultrasonic imaging (ultrasonography) uses high-frequency sound waves to create images of internal organs, which is essential for non-invasive diagnostics. In dental offices, ultrasonic scalers are used to remove plaque and tartar from teeth more efficiently than manual cleaning methods.
Additionally, ultrasonic therapy is gaining popularity for its use in pain management and wound healing. The sound waves can stimulate tissue repair by improving blood circulation and promoting faster healing.
4.3. Industrial and Manufacturing Processes
In manufacturing, ultrasonic generators are employed in processes like welding, cutting, and material testing. Ultrasonic welding uses high-frequency sound waves to join two materials, often metals or plastics, by generating localized heat through ultrasonic vibrations. This process is quick and precise, making it ideal for assembling small parts in electronics and automotive industries.
Furthermore, ultrasonic testing is used in non-destructive testing to detect flaws or defects in materials such as metals, plastics, and composites. By sending ultrasonic waves through a material and analyzing the waves that are reflected back, technicians can assess the integrity of the material without damaging it.
5. Advantages of Ultrasonic Generators
The benefits of using ultrasonic generators are extensive, making them a valuable tool across different industries. Some of the key advantages include:
5.1. Efficiency
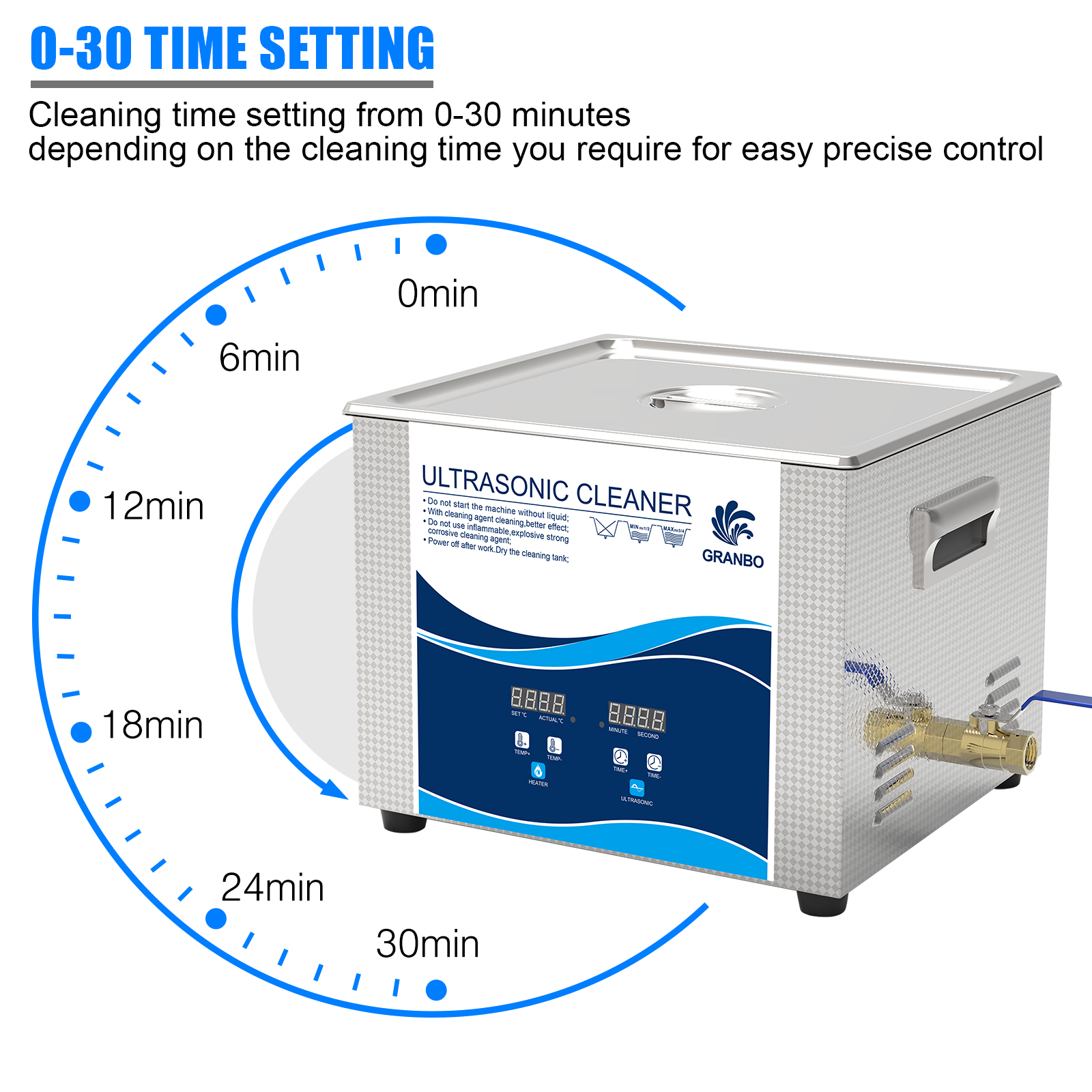
Ultrasonic generators provide a highly efficient way to carry out cleaning, mixing, and processing tasks. The high-frequency sound waves enable rapid action, significantly reducing the time needed to complete processes like cleaning or material testing compared to traditional methods.
5.2. Precision and Control
The ability to precisely control the frequency, amplitude, and duration of ultrasonic waves ensures that ultrasonic generators can be tailored to meet the specific needs of various applications. This precision is crucial when working with delicate items, such as electronics or medical instruments, where too much force or heat can cause damage.
5.3. Non-Destructive
One of the key benefits of ultrasonic technology is its non-destructive nature. In applications like material testing and cleaning, ultrasonic generators can perform tasks without causing harm to the object being treated. This makes ultrasonic cleaning ideal for items that are difficult to clean through conventional methods, such as jewelry, fine medical instruments, and electronic components.
5.4. Reduced Use of Chemicals
In many cleaning processes, ultrasonic generators eliminate the need for harsh chemicals, which not only benefits the environment but also reduces the cost of chemicals and the risks associated with their use. By using ultrasonic waves, cleaning can be achieved with water or mild solutions, making it a safer and more eco-friendly option.
5.5. Versatility
Ultrasonic generators are incredibly versatile, as they can be used in a wide variety of applications across different industries, from healthcare and food processing to manufacturing and research. Their adaptability makes them a valuable investment for many businesses, as they can serve multiple purposes without the need for specialized equipment for each task.
6. Future Trends in Ultrasonic Technology
As ultrasonic technology continues to evolve, there are several emerging trends that promise to further expand its applications and improve efficiency. One notable area of development is in the integration of ultrasonic systems with automation and artificial intelligence. By combining ultrasonic generators with robotic systems and AI, businesses can achieve higher levels of precision and automation in their operations.
Additionally, advancements in transducer technology are likely to improve the energy efficiency and frequency control of ultrasonic generators, making them even more effective and cost-efficient. This could lead to new applications in fields like pharmaceuticals, advanced manufacturing, and environmental monitoring.
Conclusion
Ultrasonic generators are a crucial part of modern industry, with applications that span from cleaning and medical treatments to food processing and non-destructive testing. The precision, efficiency, and versatility they offer make them indispensable in many fields, providing solutions that are faster, safer, and more eco-friendly than traditional methods. As technology continues to improve, ultrasonic generators will undoubtedly play an even larger role in shaping the future of various industries.
References:
- Smith, J. (2020). The Impact of Ultrasonic Technology on Industrial Cleaning Applications. Journal of Industrial Engineering.
- Liu, W. (2021). Ultrasonic Generators in Medical Diagnostics and Treatment. Journal of Medical Technology.
- Hwang, S., & Kim, B. (2022). Innovations in Ultrasonic Material Testing and Non-Destructive Evaluation. Materials Science Review.