The traditional ultrasonic cleaning method faces challenges in cleaning blind holes of components, especially those with diameters smaller than 3 millimeters and depths greater than 1 centimeter. Industrial ultrasonic cleaning machines operating at a frequency of 40kHz often struggle to meet the thorough cleaning requirements for such components, particularly for parts like casing components, motor parts, and mechanical transmission components that need to remove metal shavings and machining oils.
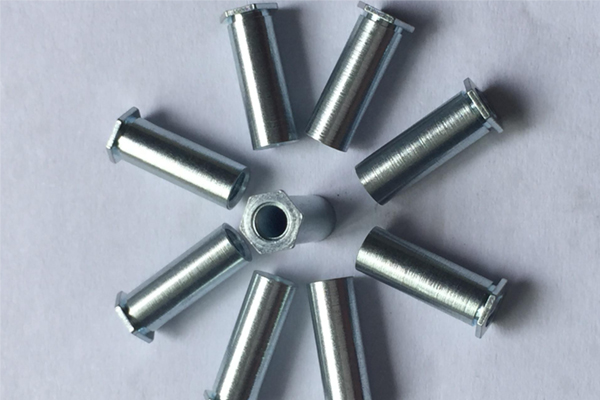
However, through technological innovation and process improvement, ultrasonic cleaning machines have effectively addressed these challenges. Here are two main solutions:
- Adding compressed air nozzles with an external air source:
In the design of industrial ultrasonic cleaning machines, compressed air nozzles can be incorporated into the cleaning tank, connected to an external air source. When cleaning components with blind holes, the parts are placed in the cleaning tank, allowing water to flow into the holes as much as possible. Subsequently, compressed air is used to generate water jets to impact the components, causing the trapped bubbles at the hole openings to rupture, thereby enhancing the ultrasonic cleaning effect.
- Using dual-frequency ultrasonic cleaning machines:
Another solution is to use dual-frequency ultrasonic cleaning machines to clean blind holes. These machines can simultaneously utilize high-frequency and mid-frequency ultrasonic waves, fully exploiting the cavitation effect generated by high-frequency ultrasonic waves and the breaking force of mid-frequency ultrasonic waves, thus thoroughly cleaning dirt and metal shavings from blind holes.
The frequency of ultrasonic cleaning machines is a key factor affecting their cleaning effectiveness. Generally, higher cleaning frequencies result in better cleaning effects. However, it’s important to avoid excessively low frequencies during the cleaning process to prevent excessive noise generation and maintain work efficiency. Therefore, selecting the appropriate cleaning frequency is crucial for achieving efficient cleaning of blind holes.
Through continuous innovation and improvement, ultrasonic cleaning technology has become an effective tool for addressing the challenges of cleaning blind holes, providing reliable cleaning solutions for industrial production.